You want strong, fast, and affordable molds for your plastic parts. Aluminum molds can help you do this. They are metal molds made from aluminum instead of steel.
Today, many engineers and product designers choose aluminum molds. Why? They are great for rapid prototyping and low-volume production. These molds are easy to machine. They also cool faster, saving you time and money.
Protolabs is a leader in aluminum tooling. They help many companies make parts quickly. In this guide, you will learn why aluminum molds are useful and how to design them well. You will also see how Protolabs supports your projects.
Why Choose Aluminum Molds?
Aluminum molds offer big benefits for your projects. Let’s explore five key reasons to pick them.
1. Faster Production
Aluminum conducts heat about 5 times better than steel. Compared to steel molds, aluminum molds offer faster processing times thanks to the greater ease of workability of the material, while maintaining adequate quality for low-volume production. Cooling makes up much of the cycle time in injection molding. Using aluminum can cut your cycle time by 25–40%, letting you make more parts every day.
2. Lower Cost
Comparatively, Aluminum molds are more cost-effective than other materials. Its overall value is dependent upon the usage of the mold, but if all other factors are constant, then the initial tool investment for Aluminum is typically lower.
3. Easy to Machine and Modify
Aluminum is softer and easier to cut than steel. Mold makers can machine aluminum at 3–10x the speed of steel. This means you get your mold faster and can apply design changes with less time and cost.
4. Good Thermal Conductivity
Aluminum molds demonstrate excellent thermal conductivity, thus enabling rapid heat transfer during the injection molding process. This particular property of rapid thermal conductivity ensures consistent and efficient cooling, which further prevents excessive shrinkage and injection molding defects such as warping. Thus, aluminum molds are well-suited for applications where precise temperature control is crucial. It also reduces the cycle time, thereby enhancing the overall productivity in manufacturing.
5. Lightweight but Durable
Aluminum weighs about one-third of steel. This makes handling easier and safer during setup. While aluminum wears faster, it still lasts for 10,000–25,000 parts—enough for prototypes or low to medium volume runs.
Rapid Heat Dissipation
Aluminum injection molds demonstrate excellent and rapid heat dissipation, which means that they can heat and cool quickly. This particular property enhances mold production efficiency.
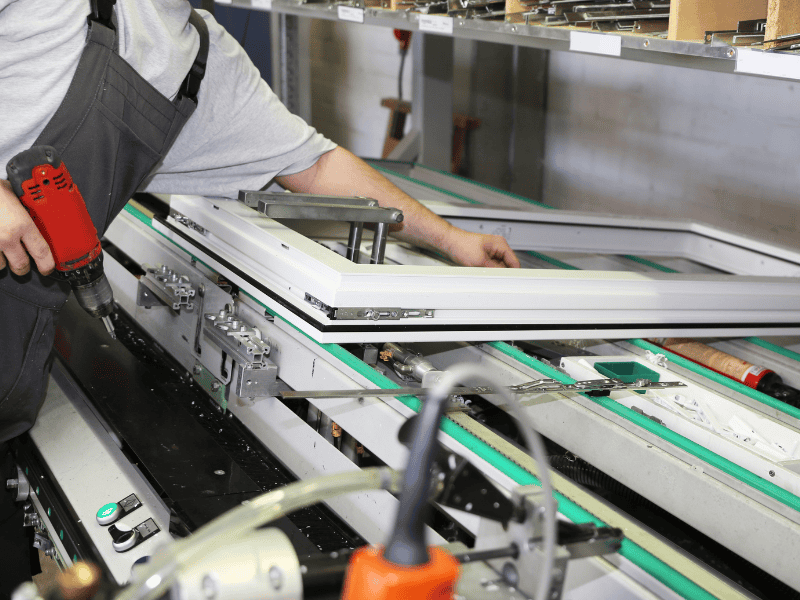
Key Design Considerations for Aluminum Molds
When you design aluminum molds, careful planning helps you avoid defects and get reliable parts. Here are five core areas to focus on:
1. Wall Thickness
You should keep the wall thickness consistent around your part. Thin sections cool fast but can warp. Thick areas take a long to cool and can cause sink marks. Aim for a uniform wall thickness between 1–3.5 mm (0.040–0.140 in) based on your plastic’s specs. This reduces cooling issues and improves part quality.
2. Draft Angles and Undercuts
Add a small taper of 1–3 degrees on vertical walls to help the part release from the mold. Deeper features may need more draft, like 2–5 degrees on tall walls or textured surfaces. Avoid undercuts if you can, or use sliders or lifters to handle them.
3. Cooling System Design
Even though aluminum cools fast, you still need a smart cooling layout. Put cooling channels near hot areas. This keeps the temperature even. It also makes cooling faster. For complex shapes, use conformal cooling. These channels follow the mold’s shape. This helps the mold cool better.
4. Surface Finishes and Texturing Limits
Aluminum molds can deliver smooth surfaces but not mirror finishes like polished steel. If your part needs a shiny face, ask the mold maker early. Most parts work well with a normal machined finish. If you want a very shiny finish, it may cost more. You might also need steel inserts for that.
5. Ejector Pin Placement
Where you place ejector pins affects part quality. Use larger-diameter pins on thick areas away from cosmetic surfaces to minimize marks. Avoid placing pins near cooling lines. Consider ejector sleeves or blades for thin walls or high-finish areas.
Why These Matter
- Proper walls and draft reduce warping and sinking.
- Smart cooling saves cycle time and cuts defects.
- Clean ejection keeps your part looking good.
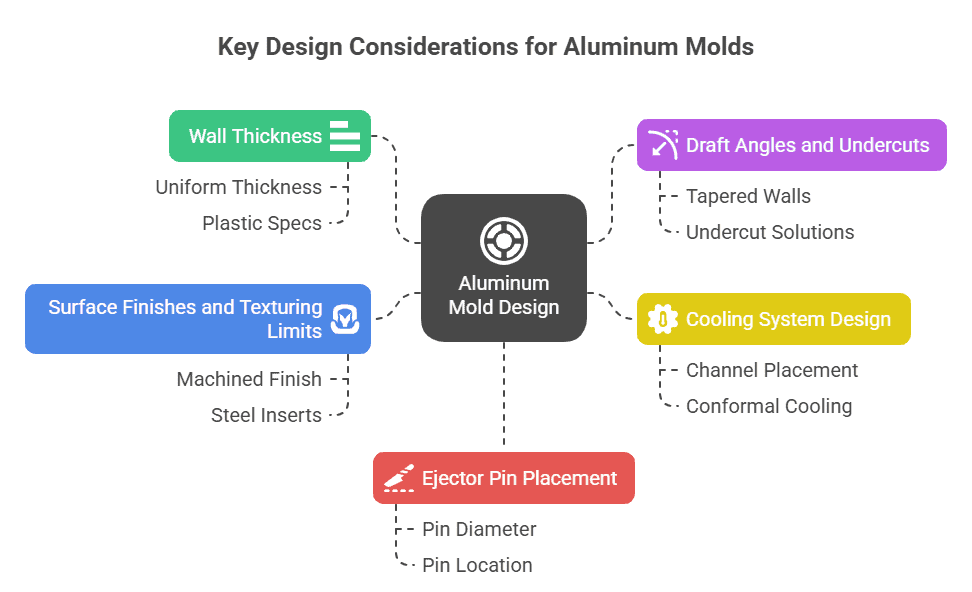
How Can Expert Manufacturers Improve Your Aluminum Mold Designs?
When you choose aluminum molds, working with experienced manufacturers makes a big difference. Companies like Huasuma specialise in metal casting, forging, and CNC machining. They focus on precision, quality checks, and strong mold designs.
For example, Huasuma uses special tools to check molds. They use chemical tests and CMM machines. These checks make sure your parts fit well. Your parts will work as they should.
Their way of working shows why experts matter. They help you avoid problems like uneven cooling or rough surfaces.
You can learn from these manufacturers. They know about aluminum types, wall thickness, and machining. Their knowledge helps you design better parts, faster.
Aluminum Tooling at Protolabs: Fast & Flexible Solutions
Protolabs offers fast, flexible aluminum tooling for prototypes and low-volume production. They combine automated quoting, design feedback, and quick mold making to help you get parts fast.
What Services Do They Offer?
Protolabs uses aluminum molds for prototyping and low‑volume runs. For small parts (under 3 × 2.5 in), they can deliver injection-molded parts in 7 days, with an option to expedite in just 1 day. For larger parts, their standard lead time is around 15 days. You also get a free design-for-manufacturing (DFM) analysis with every quote.
Lead Times and Production Scale
Their system handles both simple and complex mold designs. Small, one-cavity molds ship in 7 days; multi-cavity or large molds take up to 15 days. They support part volumes from a few units up to tens of thousands, acting as a bridge before steel tooling deployment.
Industries Served
Protolabs serves a wide range of industries, including:
- Medical devices, offering rapid prototypes for testing and approval.
- Automotive, producing parts for tests and small production batches.
- Consumer products, like cases and small tools, are made from over 100 thermoplastic resins.
Why Choose Protolabs?
- Quick turnaround time: Small parts in 1–7 days, larger molds in ~15 days.
- High-quality molds: These molds are very accurate. They can be within ±0.003 inches plus resin limits. They also get checked by CMM machines. You can ask for extra quality reports if needed.
- Easy design changes: Their online system gives free design help. You can also talk to their engineers for advice.
- Good for prototypes and bridge tooling: Aluminum molds are great for testing parts. They cost less and are safer before you buy steel molds for big production.
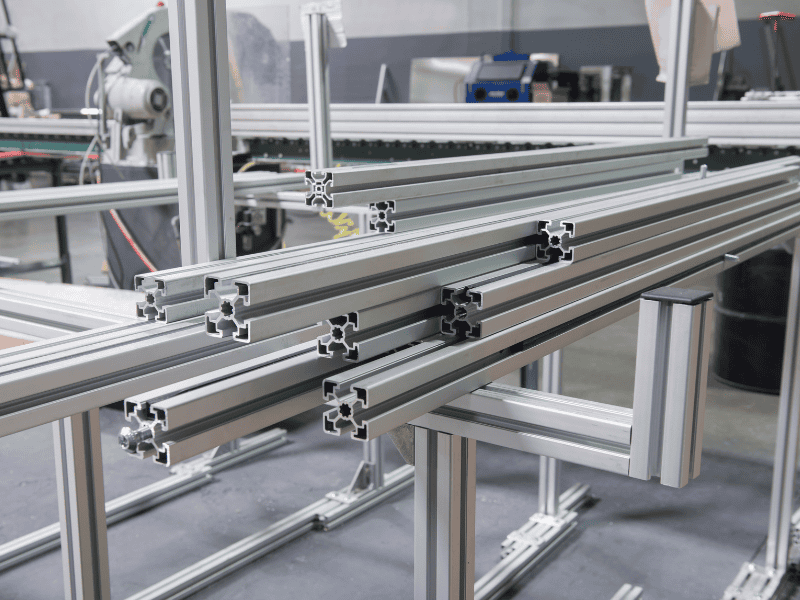
Is Aluminum Right for Your Project?
Aluminum molds are not always the best choice. Think about these points before you decide.
When to Use Aluminum Molds
Use aluminum molds if you:
- Need parts quickly for testing or market trials
- Make low to medium numbers of parts
- Want to save money on tooling costs
- Need easy changes to your mold design
Aluminum vs. Steel Molds
Here is a simple comparison:
Feature | Aluminum Molds | Steel Molds |
Cost | Lower | Higher |
Lead Time | Faster (7-15 days) | Slower (35-60 days) |
Tool Life | 10,000 – 25,000 parts | 50,000 – 100,000+ parts |
Thermal Conductivity | Better cooling | Slower cooling |
Modification Ease | Easy | Hard |
Factors to Consider
- Part Volume – For millions of parts, steel molds are better.
- Part Finish – For mirror or very fine finishes, steel is better.
- Budget & Speed – If you need fast results and lower costs, choose aluminum.
Think about these points. Then pick the mold that fits your project goals.
Conclusion
Aluminum molds help you make parts fast and save money. They are easy to machine and change. You can use them for prototypes or low-volume production. When you follow good design tips, your molds will work better and last longer.
Protolabs offers strong aluminum tooling solutions. They can help you get parts quickly for testing or use.
Ready to speed up your product development with aluminum molds? Contact us today or explore Protolabs’ aluminum tooling solutions to start your project with confidence.