Speed, flexibility, and cost-efficiency are more critical in today’s manufacturing landscape than ever. Whether you are prototyping a new part or running a short production cycle, aluminum molds have emerged as a game changing solution. Known for their rapid turnaround, lower tooling costs, and superior thermal conductivity, aluminum molds are especially valuable for rapid prototyping and low-volume production.
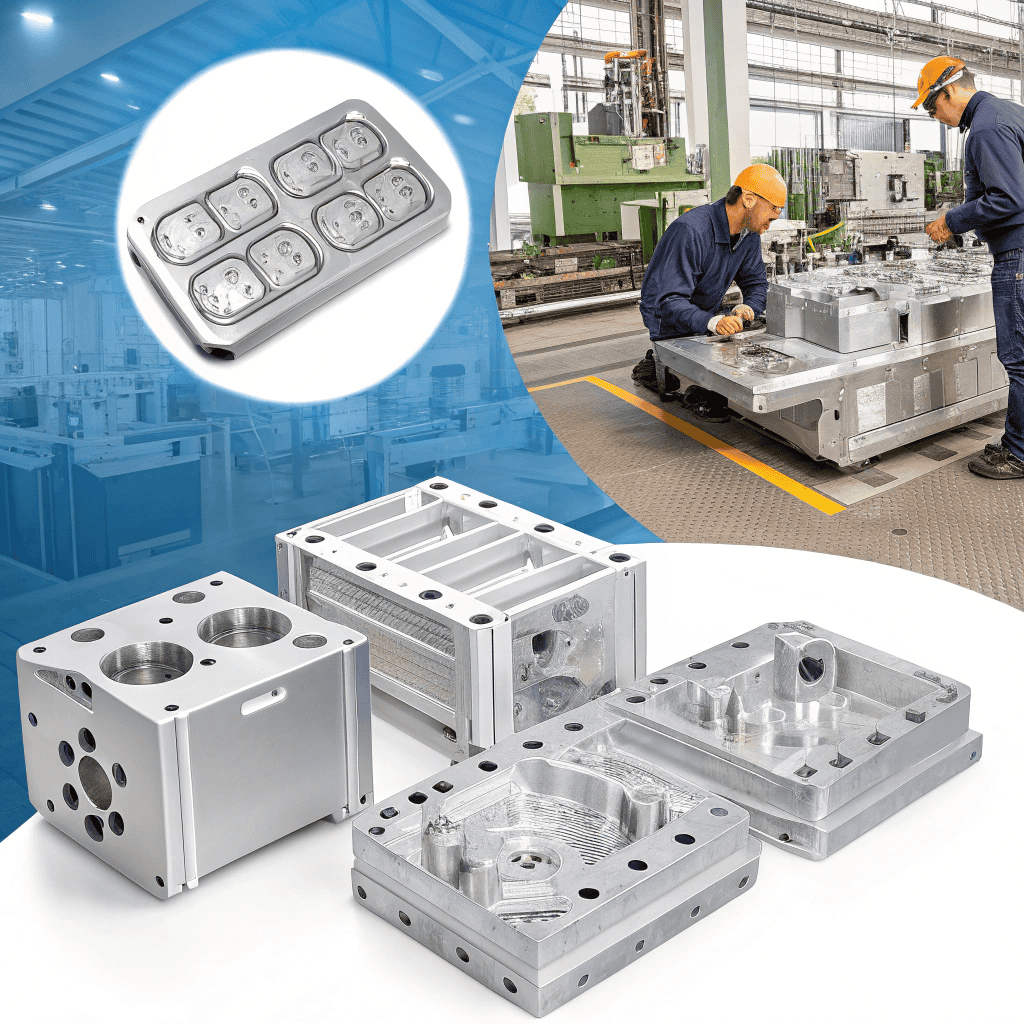
This guide outlines the key benefits of aluminum mold tooling, offers practical design considerations, and highlights Hanke Construction’s capabilities in delivering high-precision, fast-turnaround tooling solutions.
Aluminum Mold Tooling : Smarter Choice for Fast, Cost-Effective Molding
When it comes to creating parts quickly, affordably, and efficiently, aluminum mold tooling is becoming the go-to choice for engineers and product developers. Whether you are prototyping a new design or launching a small-batch product, aluminum molds offer speed, flexibility, and cost savings that traditional steel molds often can’t match.
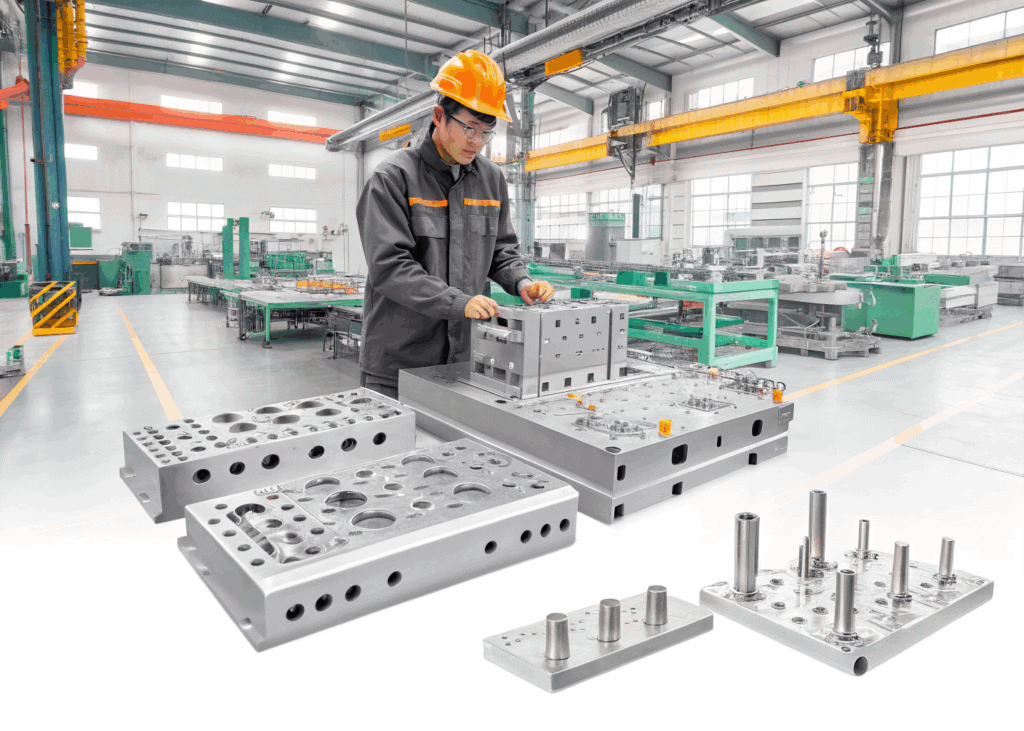
Here are the key benefits of aluminum molds, share essential design considerations for aluminum molds, and highlight how aluminum tooling at Hanke Machinery is helping businesses accelerate production.
What Is Aluminum Mold Tooling?
Aluminum mold tooling refers to using aluminum to manufacture the molds used in the plastic injection molding process. These aluminum molds are lighter and easier to machine than traditional steel molds, making them ideal for rapid prototyping and low- to mid-volume production. While they don’t match steel in long-term durability, their speed and cost-efficiency offer major advantages in early-stage development.
Why Choose Aluminum Molds?
Aluminum molds provide value beyond prototyping. Instead of choosing steel molds for high-volume production, consider aluminum molds instead. They prove to be a cost- and time-effective solution.
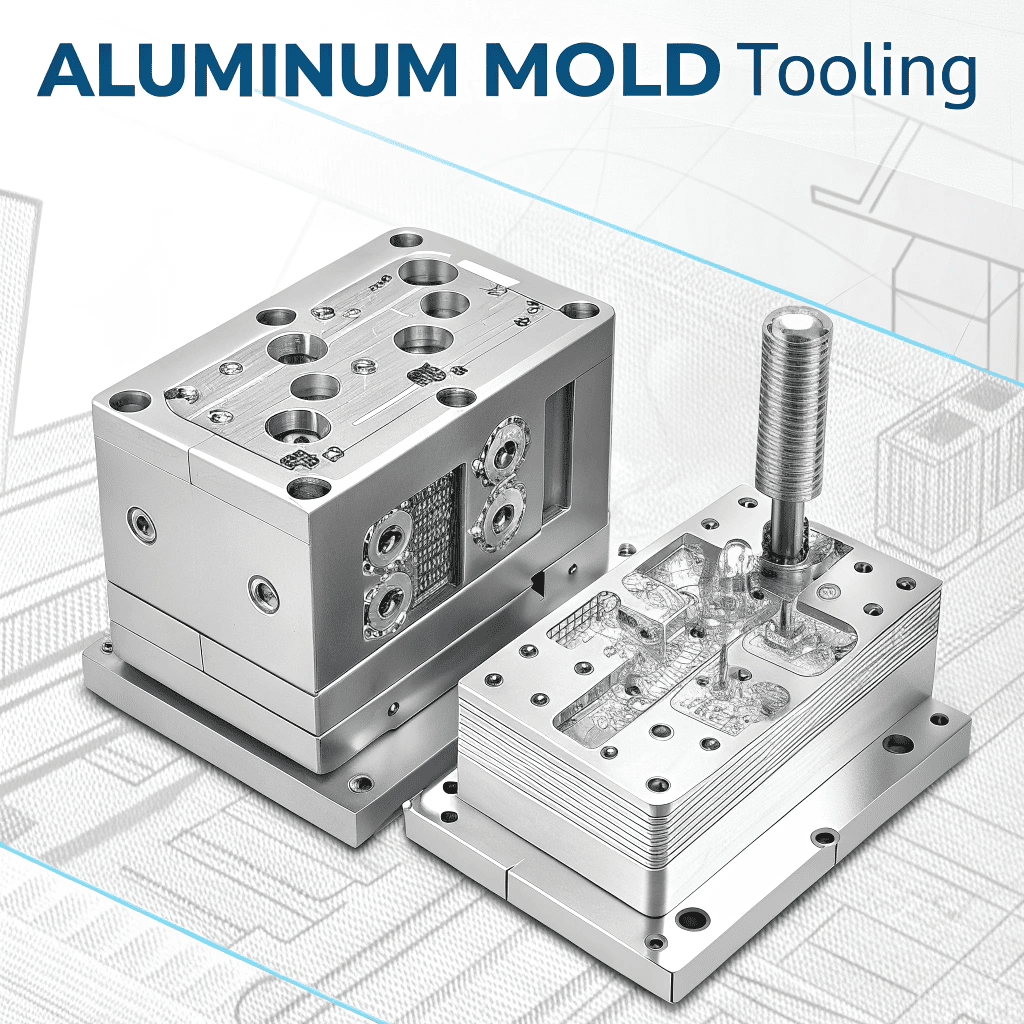
The primary advantage of using aluminum for tooling lies in its ability to create cost-effective molds for low-volume injection molding. Aluminum is easy to machine and offers excellent thermal conductivity, allowing for faster cooling rates and significantly reduced cycle times, ultimately lowering production costs for OEMs.
Once the aluminum mold is prepared, part production for rapid prototyping can begin almost immediately. However, to fully leverage the benefits of aluminum tooling, expert knowledge and experience are essential in maximizing its potential in rapid prototyping applications.
For example, 7075 aluminum can produce tens of thousands of parts when designed correctly, making it more durable than most assume. However, careful material selection and tooling practices are key.
- Speed of Production
One of the most significant advantages of aluminum molds is the dramatic reduction in production time. Aluminum is easier to machine than steel, allowing mold production to be completed in a matter of days rather than weeks. This makes aluminum tooling ideal for fast-paced development cycles.
Superior thermal conductivity also plays a role in speeding up the injection molding process. Aluminum molds cool more quickly, which results in shorter cycle times and higher throughput.
- Cost-Effectiveness
Aluminum mold tooling is significantly more cost-effective than steel, particularly for low-volume production and prototyping. Tooling costs can be reduced by 20–40%, making it an economical choice for testing new designs or launching limited product runs.
- Easier Machining and Modifications
Aluminum is a softer material compared to steel, which allows for quicker and easier modifications. If a design change is required, it can be implemented rapidly without significant downtime, helping teams stay agile.
- Excellent Thermal Conductivity
The thermal properties of aluminum not only speed up the cooling process but also improve mold performance. The material ensures even temperature distribution throughout the mold, reducing the risk of warping or sink marks and enhancing part consistency.
Cooling times can be reduced by up to 50%, significantly impacting overall production efficiency.
- Lightweight Yet Durable
While aluminum molds aren’t suited for high-volume runs exceeding 100,000 cycles, they are ideal for short runs and prototyping. Their lightweight nature makes them easier to handle, install, and transport, which also contributes to faster changeovers and improved operational safety.
Here are some Additional Benefits of Aluminum Mold Tooling
- Design Flexibility: Aluminum’s machinability supports more complex part geometries and fine details, making it well-suited for intricate designs and multi-cavity molds.
- Environmental Friendliness: Aluminum is fully recyclable and supports sustainability goals. Using aluminum molds contributes to greener manufacturing practices by reducing waste and supporting a circular economy.
- Custom Finishes: While not as polished as steel, aluminum molds can still support a variety of surface textures, from matte to semi-gloss. With proper planning, cosmetic standards can be achieved cost-effectively.
- Quick Prototyping: Because aluminum molds can be designed and built so rapidly, they are perfect for short-run production and iterative testing. Product teams can validate and refine their ideas quickly, saving time and money.
Aluminum molds demonstrate better thermal conductivity, flow rate, and fill advantages over steel molds. Which makes aluminum a better option when you are producing long, large parts.
These combined benefits show why aluminum mold tooling has become the go-to option for modern manufacturing workflows that demand speed, cost-efficiency, and flexibility.
Key Design Considerations for Aluminum Molds
Designing for aluminum mold tooling requires a thoughtful approach to maximize durability and performance. As a professional aluminum die casting manufacturer, Hanke Constructions would like to share some main design considerations for aluminum mold tooling and provide tips to help you optimize your designs for this process. Here are the key areas to focus on:
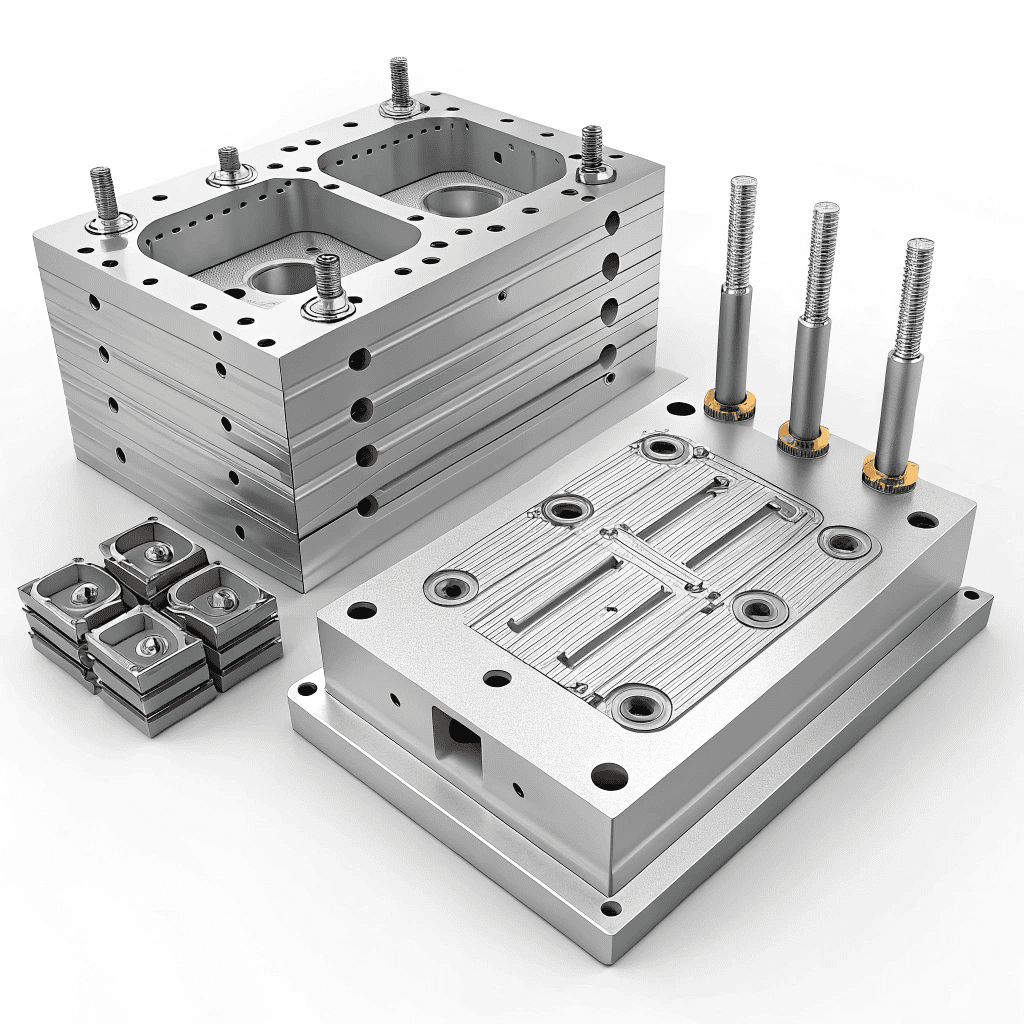
- Wall Thickness Optimization
Maintaining uniform wall thickness is crucial in aluminum mold design. Irregular thickness can lead to uneven cooling, which increases the risk of warping or part defects.
- Draft Angles and Undercuts
Draft angles are important because they make it easier to remove parts from the mold. Because aluminum is softer than steel, incorporating generous draft angles reduces stress on the mold and increases its lifespan. Minimize complex undercuts that may require sliders or side actions.
- Cooling System Design
Due to aluminum’s natural heat dissipation capabilities, elaborate cooling systems may not be necessary. However, designers should still ensure the mold facilitates even cooling across all areas.
- Surface Finish and Texturing
While aluminum molds can support a range of surface finishes, they are not as resistant to wear as steel. For high-gloss or heavily textured surfaces, it is important to set realistic expectations or consider using hybrid molds.
- Ejector Pin Placement
Because aluminum is more prone to wear, improper ejector pin placement can damage the mold over time. Designers must ensure that the ejection system is properly aligned and balanced to prevent long-term damage.
Aluminum is lighter than steel and gives you more volume for less cost. And so aluminum gives you more molds for the same money.
Aluminum mold tooling offers many benefits for the production of high quality parts, but it is crucial to consider several design factors to achieve optimal results.
Aluminum Tooling at Hanke Construction: Fast & Flexible Solutions
Overview of Services
Hanke Construction Machinery Manufacturing Co., Ltd is a leading provider of high-precision aluminum mold tooling solutions. Their services are designed to support prototyping, bridge production, and low-volume manufacturing with exceptional turnaround times and quality.
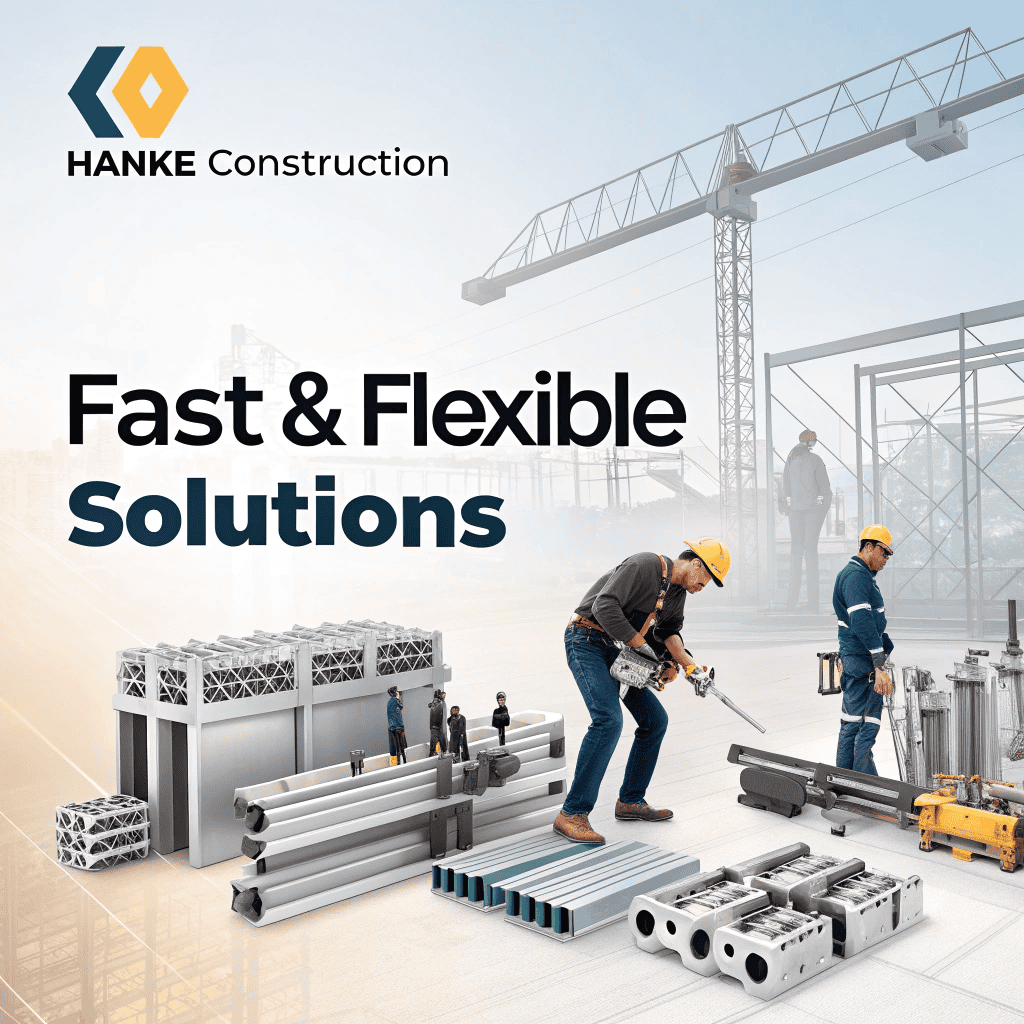
Capabilities and Lead Times
Hanke’s aluminum tooling capabilities include custom mold design, CNC machining, and rapid prototyping. With efficient workflows and advanced equipment, typical lead times range from 1 to 15 days, depending on project complexity and requirements.
Industries Served
Hanke supports clients in a variety of sectors, including:
- Medical and Healthcare: Prototypes and enclosures for medical equipment
- Automotive: Lightweight parts, trims, and functional prototypes
- Consumer Electronics: Enclosures, buttons, and accessories
- Industrial Equipment: Precision plastic components for tools and machines
Why Choose Hanke?
- Fast production and on-time delivery
- Competitive pricing for low to mid volume runs
- Custom solutions tailored to part complexity
- Quality assurance and precision manufacturing
- Experience in both domestic and international markets
With deep industry experience and a commitment to quality, Hanke is a reliable partner for your aluminum tooling and prototyping needs.
Is Aluminum Right for Your Project?
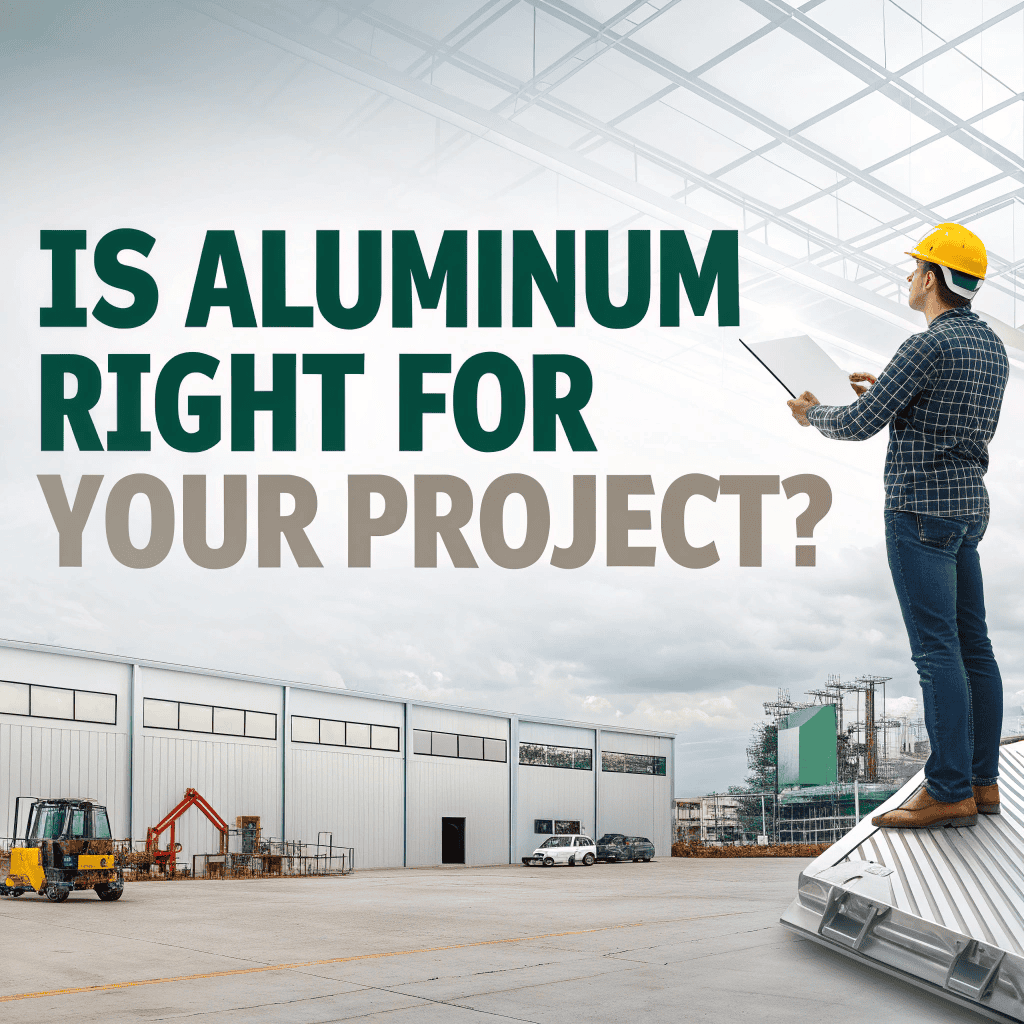
Aluminum molds are best suited for situations where speed, flexibility, and cost-efficiency are top priorities. Here is when you should strongly consider aluminum:
Rapid Prototyping & Iterative Design
One of the most common uses of aluminum molds is for prototyping. Whether you’re validating a product idea or conducting functional testing, aluminum molds allow fast turnaround and easy design changes. Iterations that might take weeks with steel tooling can often be completed in days with aluminum.
Short-Run or Low-Volume Production
For runs up to 10,000 parts, aluminum is ideal. It allows businesses to quickly enter the market with low upfront costs. This is particularly useful for:
- Seasonal products
- Crowdfunded launches
- Niche market trials
- Customized or regional variants
Bridge Tooling Before Full-Scale Production
Aluminum molds are often used as a “bridge” to full-scale production. You can get to market faster while steel tooling is still being developed. This approach reduces risk and allows early revenue generation while your main tooling investment is being finalized.
Budget-Conscious Projects
If budget is a concern, aluminum molds are an easy win. Not only is the tooling cheaper (by 20–40%), but the overall project cost (including energy, labor, and downtime) is typically reduced by as much as 30%.
Choosing between aluminum molds and steel molds depends on several factors:
Criteria | Aluminum Molds | Steel Molds |
Cost | Lower | Higher |
Lead Time | 1–2 weeks | 3–6 weeks |
Production Volume | Low to Medium (<10,000) | High (>100,000) |
Modification Flexibility | Easy and quick | Time-consuming |
Thermal Conductivity | Excellent | Moderate |
Surface Finish Capability | Moderate | Excellent |
Weight | Lightweight | Heavy |
Ideal Use Cases for Aluminum Molds
- Rapid prototyping
- Market testing or MVP launches
- Seasonal or custom product runs
- Bridge tooling before full-scale production
If your project values speed, agility, and cost-efficiency over long-run durability, aluminum mold tooling is likely your best choice.
Longevity Tips for Aluminum Injection Mold Tooling
While aluminum molds are best known for prototyping, their lifespan can be extended with careful design and usage. When used strategically, they can even serve as bridge tools for limited production runs.
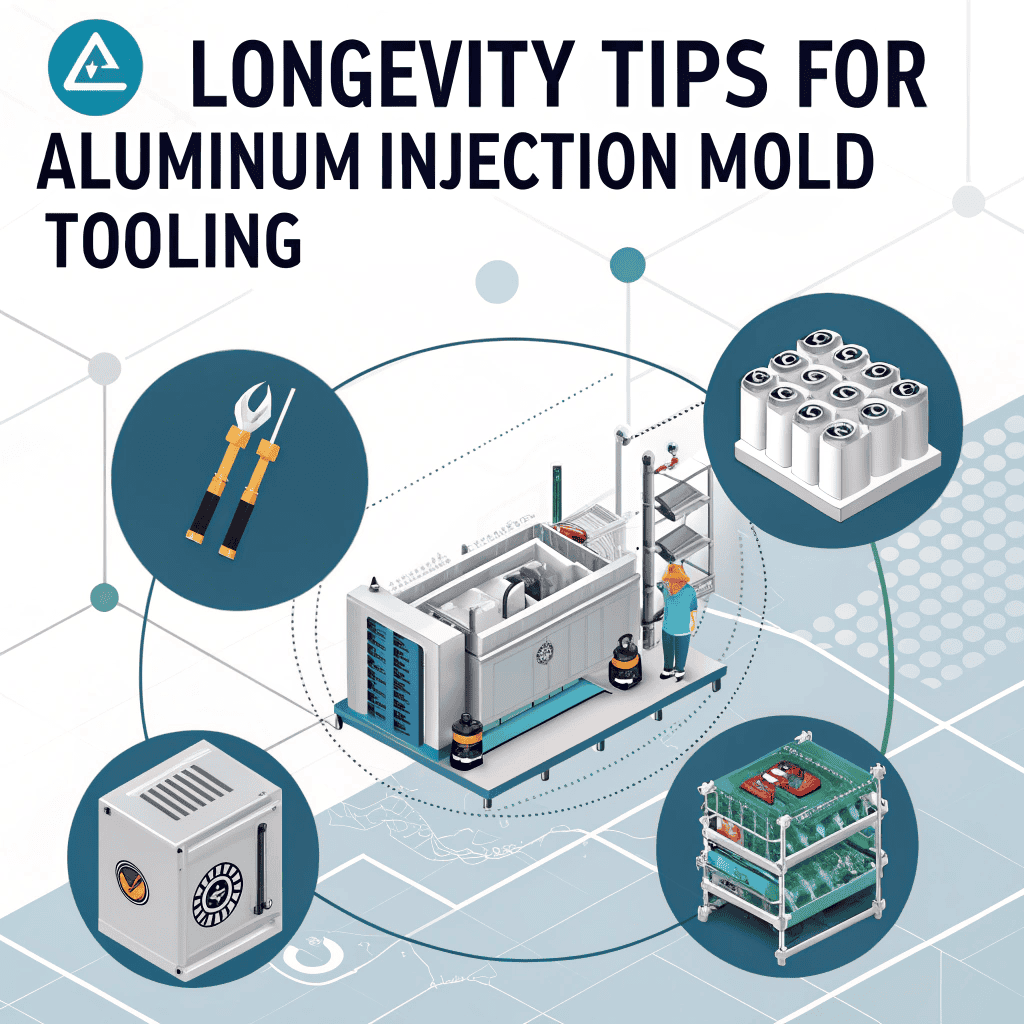
Keep in mind:
- Aluminum is softer than steel, making it unsuitable for high-volume production.
- Polishing is challenging, so it’s better suited for functional parts than cosmetic finishes.
- Repairs are more difficult, so it is ideal for rapid prototyping and proof of concept runs rather than long-term use.
Conclusion
Aluminum molds present a versatile and highly efficient solution for engineers, product developers, and manufacturers aiming to prototype or produce low to mid-volume parts with speed and cost-effectiveness. Their superior thermal conductivity enables faster cooling cycles, significantly reducing lead times compared to traditional steel molds. Additionally, aluminum molds are easier to machine and modify, allowing for quick design changes and iterative improvements.Hanke Construction Machinery Manufacturing Co., Ltd stands out as a trusted provider of high-quality aluminum molds and precision tooling solutions. With a commitment to advanced manufacturing techniques and customer-centric service, Hanke delivers reliable, durable, and performance-oriented mold products that meet the evolving needs of modern production environments. Whether for prototyping or low-volume production, Hanke’s expertise ensures that customers receive efficient, tailored solutions that enhance productivity and reduce time to market.