Water glass sand casting, also called the sodium silicate process, is a popular way to make metal parts. It uses sodium silicate to form strong molds. These molds can handle high heat and hold their shape well during casting.
This method is common in industries that need accurate and large metal parts. You’ll see it used for cast steel, cast iron, and alloy components in tools, machinery, and auto parts.
But like all methods, this one comes with challenges. Aging, surface chalking, and moisture absorption can affect the final product. If not handled well, they can lower strength and ruin surface quality.
In this guide, you’ll learn how the process works, why these issues matter, and how to solve them. You’ll also see the key characteristics, pros and cons, and tips to get better results from your water glass sand casting work.
Overview of Water Glass Sand Casting
Water glass casting is also called sodium silicate casting. Its casting process is very similar to investment casting (that is the lost wax investment casting method). It is a technology that uses water glass as the binder for the shell to cast.
The process provides a far superior surface finish and dimensional precision to that achieved through sand casting. And more complex shapes can be achieved. The global sodium silicate market size was valued at $8 billion in 2023, and is projected to reach $12.7 billion by 2033, growing at a CAGR of 4.9% from 2024 to 2033.
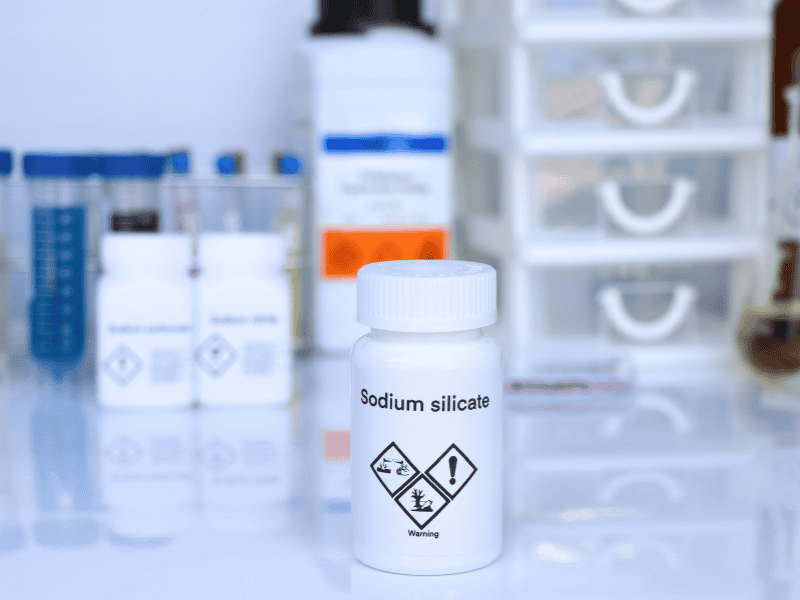
Step 1: Wax Injection
You start by injecting melted wax into an aluminum mold. This creates a wax copy of the final part. The mold is sized to allow for shrinkage of both the wax and the metal. Some molds are simple. Others are complex and may use water-soluble or ceramic cores. Some even have many cavities to make more than one part at a time.
Step 2: Wax Assembly
Next, you take the cooled wax patterns and attach them to a wax rod. This rod is called a sprue. It holds everything together and allows molten metal to flow to each part later. The sprue also includes paths (called gates and runners) to feed the metal into the mold.
Step 3: Shell Making
Now, you coat the wax pattern with a ceramic shell. First, dip the wax into a liquid ceramic. Then sprinkle it with dry sand. Let it dry. You repeat this several times until the shell becomes strong and thick. Shell building usually takes about one day. But the drying can take from two days to a full week.
Step 4: Dewaxing
Once the shell is dry, you heat it. This melts and removes all the wax inside. The heat also hardens the ceramic shell. After this, the mold is empty and ready for metal.
Step 5: Pouring
You heat the ceramic shells again before pouring. At the same time, melt the metal and make sure it’s clean. Then, pour the hot metal into the shell while it’s still warm. This helps fill the mold properly.
Step 6: Finishing
The shell is hammered, media blasted, vibrated, waterjet, or chemically dissolved (sometimes with liquid nitrogen) to get the finished casting. The sprue is cut off and recycled. The casting may then be cleaned up to remove signs of the casting process. Usually by grinding.
Where It’s Used
Water glass cast components are mainly used for heavier or stronger, more complex shapes products.
These applications are in the field of trailers, agricultural machinery, and the offshore industry.
For example:
- Automotive – parts like manifolds, brackets, and housings
- Machine tools – gears, arms, and bases
- Construction – hardware parts and heavy equipment
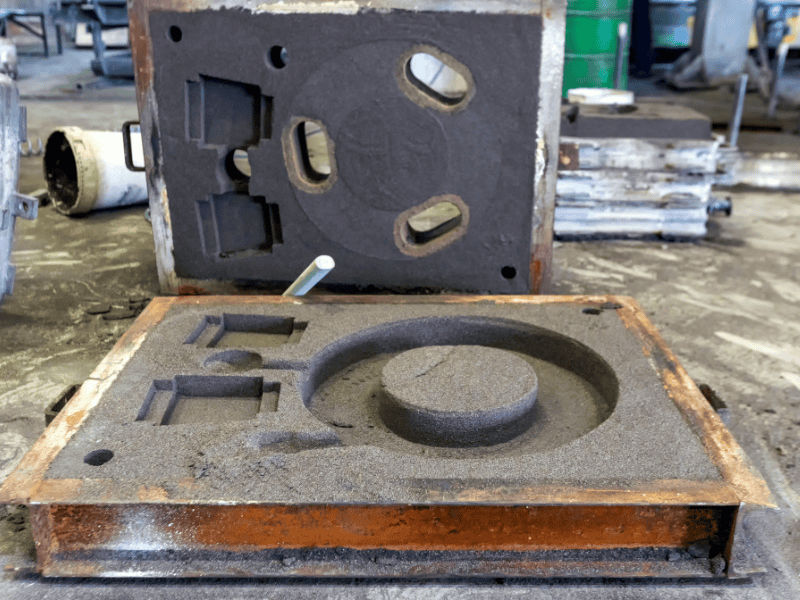
Aging in Water Glass Sand Casting
In water glass sand casting, aging means the mold or finished casting changes over time. This change happens after the mold is made or the part is cast. It affects the quality, strength, and surface finish of the final product.
How Aging Affects Sand Molds and Castings
As molds age, they absorb moisture and weaken. The bonding strength between the sand particles gets lower. This makes the mold more fragile.
If the mold ages too long before casting, the metal might not form the right shape. It could lead to cracks, surface defects, or poor dimensional accuracy.
Aging can also affect the final part. If stored too long in the open air, castings can become chalky, brittle, and even warp over time.
Common Causes of Aging
- Time – The longer the mold or part sits, the more likely aging will occur.
- Humidity – Molds absorb water from the air. This weakens the bond.
- Temperature – High heat speeds up chemical reactions that lead to breakdown.
Even short exposure to moist air or sunlight can cause damage if not stored properly.
What Happens to the Casting?
- The surface can become rough or powdery.
- Strength and hardness can drop.
- Shape may change slightly, making it harder to fit or function.
- Cracks may form, especially in thin or detailed areas.
Aged parts don’t last as long and may fail early in real use.
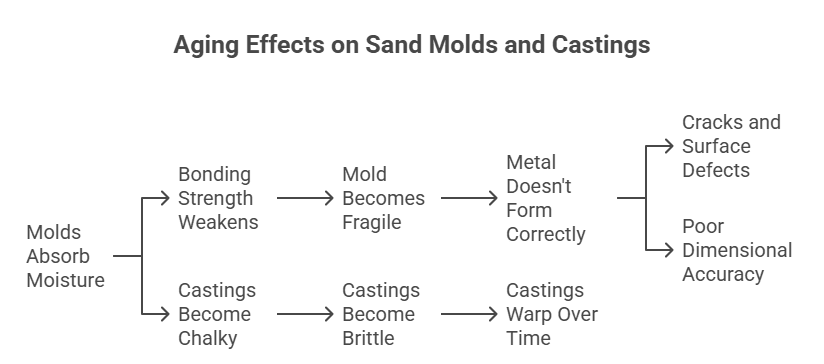
Surface Chalking in Water Glass Sand Casting
Surface chalking happens when a white, powdery layer forms on the surface of your castings. It looks like dust or dried salt. You can rub it off with your finger, but it keeps coming back if not treated.
This is a sign that your casting is breaking down on the outside.
What Causes Surface Chalking?
Chalking is caused by moisture and carbon dioxide in the air. These react with leftover sodium silicate in the mold or on the surface of the casting.
When the part sits in humid air, water and CO₂ react with the sodium silicate to form silicic acid. This breaks down into a soft, chalky layer. Over time, the layer spreads and weakens the outer surface.
Why Surface Chalking Is a Problem
- It makes the surface look poor.
- It can weaken the outer layer, leading to cracks.
- It may affect paint, coatings, or bonding with other materials.
- It’s a sign that your mold or part was not stored or dried correctly.
If you’re shipping or using cast parts for high-precision work, chalking can cause failure or rejection.
How to Detect Surface Chalking
- Look for white spots or streaks on the casting surface.
- Rub a finger across the surface—if powder comes off, it’s chalking.
- Measure the surface strength. A soft or dusty feel means chalking has started.
How to Prevent Surface Chalking
- Store molds and castings in dry areas. Keep them away from moisture and open air.
- Cure the molds properly. Make sure the sodium silicate fully hardens before use.
- Use protective coatings. A thin barrier can block moisture and CO₂.
- Control humidity and temperature in your work area or warehouse.
- Check molds before use. If a mold looks chalky, replace it.
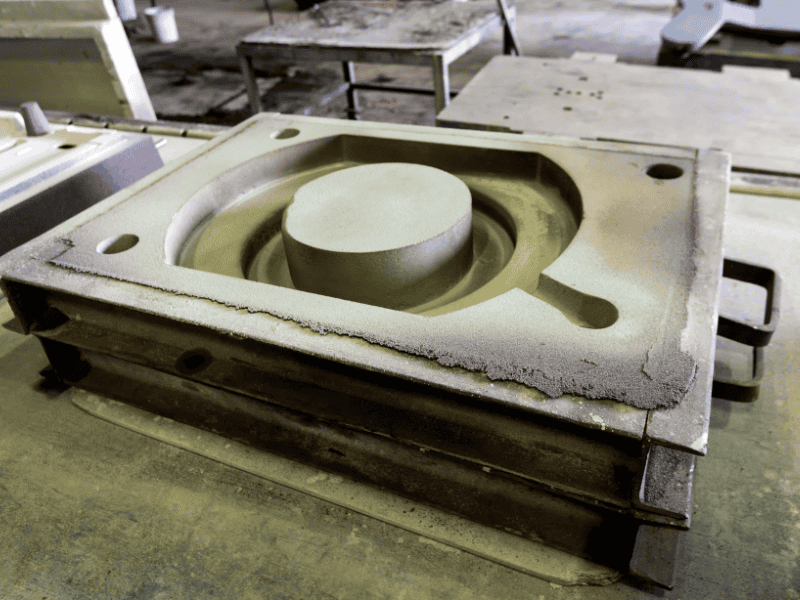
How to Improve the Moisture Absorption Resistance
Moisture is one of the biggest threats to water glass sand molds. When molds absorb too much water, they lose strength, shape, and surface quality. To keep your castings strong and stable, you need to improve the moisture absorption resistance of your molds.
Why Moisture Resistance Matters
Water weakens the bond between sand and binder. It can also cause mold swelling, cracking, or early breakdown during casting. This leads to:
- Warped or damaged castings
- More surface defects
- Lower strength and durability
If you want clean, strong results, your molds must resist moisture well—both during and after curing.
Ways to Improve Moisture Resistance
1. Use Additives and Binders
Add certain materials to make your molds tougher:
- Zinc oxide helps form stronger, water-resistant bonds.
- Calcium chloride and aluminum salts reduce water absorption.
- Polyacrylamide boosts bonding and reduces water uptake.
- Plasticizers like glycerin add flexibility and help hold shape.
These additives reduce water damage and increase mold life.
2. Choose Better Hardening Methods
The way you cure the mold affects its resistance:
- Oven drying gives better strength than air drying.
- Heat curing at 100–150°C drives out water fully.
- Avoid under-curing, which leaves moisture trapped inside.
Proper hardening improves structure and stops early breakdown.
3. Improve Storage and Handling
Moisture can still reach cured molds. Store them the right way:
- Keep them in a dry, cool room
- Use sealed bins or moisture-proof bags
- Don’t stack molds too tightly (airflow matters)
- Limit storage time to reduce aging
If you reuse molds, inspect them first. Moisture damage isn’t always visible.
4. Apply Protective Coatings
Spray-on coatings help stop water from entering the mold:
- Use ceramic sprays or sealants
- Make sure the coating is dry before use
- Reapply if stored for a long time
This small step can greatly improve moisture resistance.
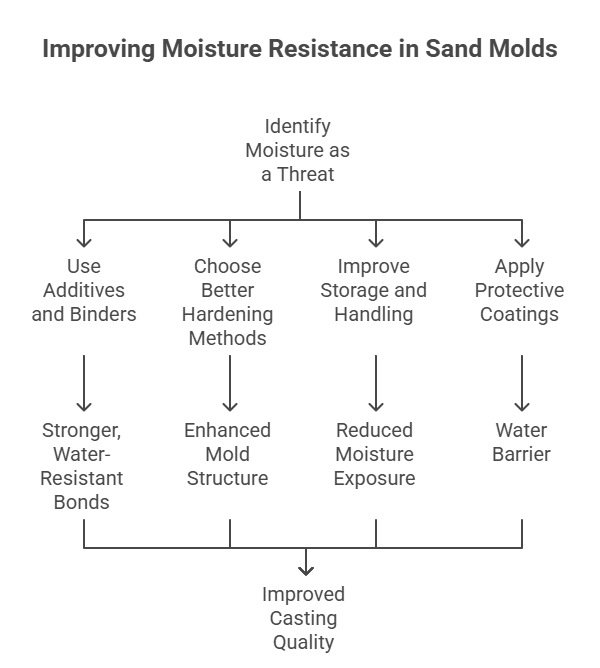
Key Characteristics of Water Glass Sand Casting
Water glass sand casting has many useful characteristics. These features make it a strong choice for casting large or detailed metal parts.
Mechanical Properties: Strength and Hardness
When cured properly, molds made with sodium silicate are hard and strong. They can handle the heat and weight of molten metal.
The cast parts also have good compressive strength, which means they won’t easily crack or bend under pressure.
But over time, if not stored well, strength can go down due to aging or moisture.
Thermal Properties: Heat Resistance and Conductivity
This method can handle high temperatures, making it useful for cast iron, steel, and other metals that melt at very hot levels.
The sand and sodium silicate mix can resist heat without breaking or melting. It also has low thermal conductivity, meaning it doesn’t let heat pass through too quickly. This helps keep mold shapes steady during pouring.
Dimensional Stability
Water glass molds keep their shape well during casting. This gives you accurate parts with tight dimensions.
If you need parts that must fit together without extra work, this is a good method.
But remember: moisture or aging can change the mold shape, so storage matters.
Surface Quality
This process gives you a smooth surface finish. Not as smooth as investment casting, but much better than regular green sand casting.
If surface quality is important for your part, water glass casting gives a good balance of cost and finish.
Environmental Considerations
Sodium silicate is non-toxic and doesn’t give off harmful fumes during casting. That makes it safer for workers and better for the environment than many other binders.
Also, the leftover sand can often be recycled after casting, depending on your process.
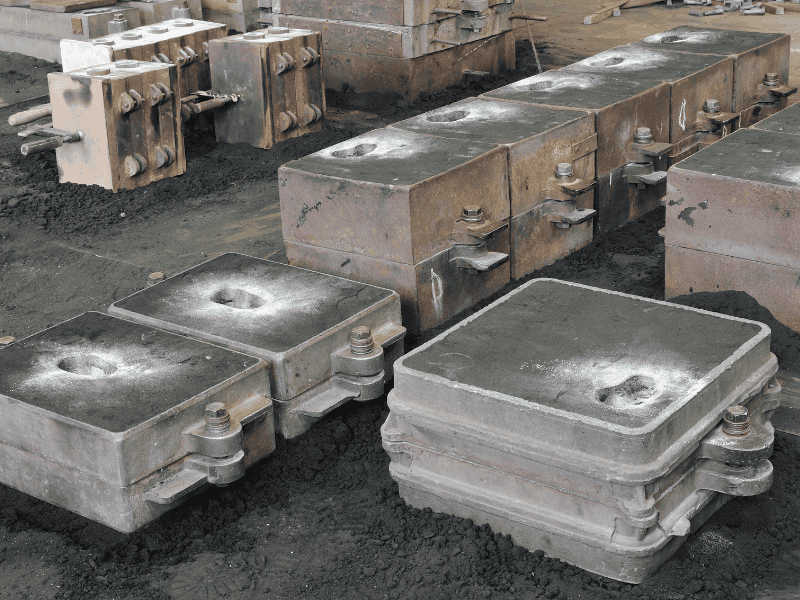
Pros and Cons of Water Glass Sand Casting
Before you choose water glass sand casting, it’s good to know the pros and cons. This helps you decide if it’s right for your job.
Pros
1. Low-Cost Molding
You don’t need expensive tools or materials. The sodium silicate and sand are easy to get and affordable.
2. Easy to Find Materials
Sand and water glass are common in most places. You won’t struggle to find supplies.
3. Good Dimensional Accuracy
This method gives you accurate shapes. You get less shrinkage and fewer errors compared to basic sand casting.
4. Great for Medium to Large Castings
If your part is big or heavy, this process works well. The molds are strong and can hold their shape even with molten metal inside.
Cons
1. Surface Finish Not the Best
While better than green sand casting, it’s not as smooth as investment casting. You may need more polishing.
2. Lower Mechanical Properties
Parts made this way can be a little weaker than those made with high-end casting methods. They may not handle stress as well.
3. Sensitive to Moisture
Water can weaken molds. You need dry storage and good control of humidity to avoid mold damage or surface chalking.
4. Risks from Aging and Chalking
If you wait too long before using a mold, aging can reduce strength. Chalking may also show up on old or poorly stored castings.
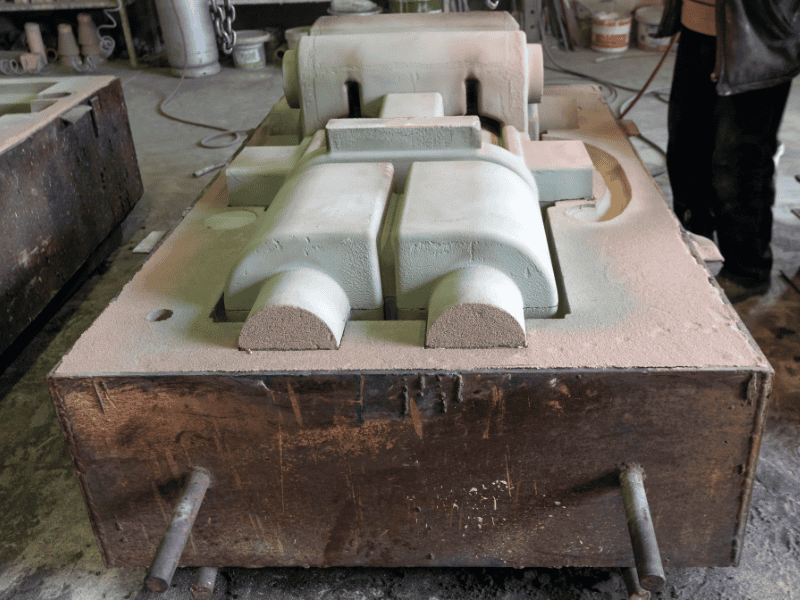
Best Practices and Recommendations
To get the best results from water glass sand casting, you need the right materials, setup, and care. Follow these tips to reduce problems and make strong, clean castings.
Choose the Right Materials and Process Settings
- Pick the right type of sand—fine sand gives smoother finishes, while coarse sand offers more strength.
- Use fresh sodium silicate. Old or exposed binder can lose strength.
- Keep the SiO₂/Na₂O ratio within the right range for your job. This helps control hardening speed and mold stability.
Keep Molds Dry and Stable
- Cure your molds properly. Use oven drying or CO₂ hardening to make sure they’re fully set.
- Store molds in a cool, dry place. Moisture and heat can ruin them.
- If you’re not using the molds right away, wrap or seal them to block air and water.
Prevent Aging and Chalking
- Don’t let molds or castings sit too long before use.
- Use coatings to protect finished parts from moisture and CO₂.
- Check castings for white powder (chalking) or soft spots before moving to the next step.
Reduce Defects During Casting
- Preheat the mold if the room is cold. This avoids cracks when pouring hot metal.
- Don’t use damaged or aged molds. Small cracks can grow during casting.
- Keep metal pouring steady. Fast or uneven pouring can cause air pockets or poor filling.
Know When to Use This Process
Water glass sand casting is best when you need:
- Medium to large metal parts
- Good accuracy but not perfect surface quality
- Lower cost and faster turnaround than high-end methods
Avoid it if your part needs:
- Very smooth surface
- High impact strength
- Tight mechanical tolerances without extra finishing
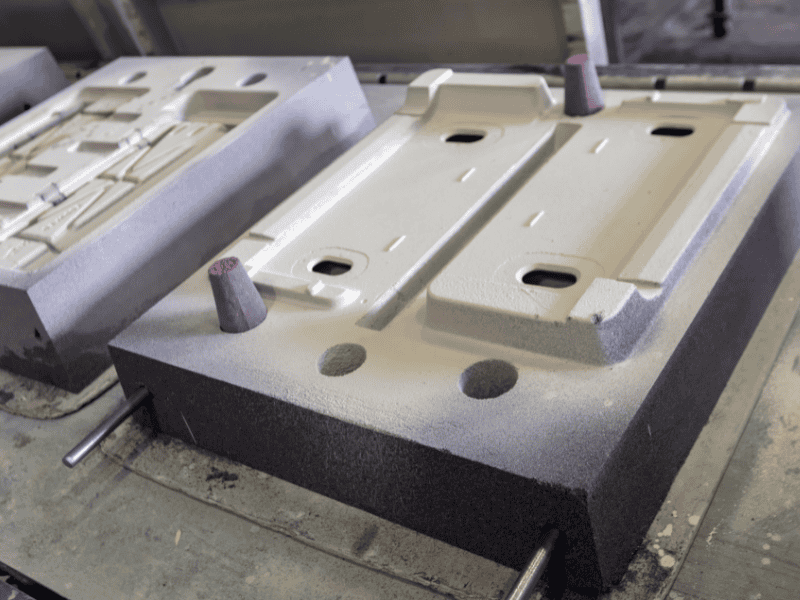
How Industry Leaders Apply These Techniques
It helps to see how these casting and machining ideas work in real life.
One example is Huasuma. They are a company in China that makes metal parts. They work with casting, forging, and CNC machining. They also share helpful guides and case studies on their website.
Their content explains how to choose the right materials and how to design molds. It also shows how to control the process to make better parts. This helps people avoid mistakes and improve quality.
Huasuma works with many industries. These include car making, building, and mining. By looking at what they do, you can learn how these ideas are used every day in real factories.
Conclusion
Water glass sand casting is a smart choice for many metal parts. It’s simple, cost-effective, and works well for large or complex shapes.
But to get good results, you need to manage key problems like aging, surface chalking, and moisture absorption. These can damage your molds and weaken your castings if ignored.
You’ve learned the key characteristics, the pros and cons, and how to improve mold quality. You’ve also seen the best ways to avoid common mistakes and extend the life of your castings.
Want to see how manufacturers apply these methods to real projects? Review technical resources from companies like Huasuma to understand how casting and machining principles are used. Studying actual workflows and results can help you make better decisions for your own designs or processes.