Do you want liners that last longer and work better? This guide to the alloy steel liner manufacturing process will help you understand how they are made.
Alloy steel liners are strong. They can handle heat, wear, and heavy impact. That’s why they are used in machines like mills, crushers, and chutes.
In this article, you’ll learn what alloy steel liners are, how they are made step by step, and what materials are used. You’ll also see how they compare to other liners and how we check their quality.
Let’s begin.
What Is an Alloy Steel Liner?
Alloy steel liners are tough metal plates used to protect machines that crush, grind, or move heavy materials. You’ll often see them inside mills, crushers, and chutes in industries like mineral processing and power generation.
These liners stop the machine parts from wearing out too fast. The steel they’re made of is mixed with other metals to make it stronger. This is why they’re called alloy steel. Common uses include ball mills in mining, crusher chambers in quarries, and feed chutes in cement plants.
Why Choose Alloy Steel Liners?
You use alloy steel liners because they give high wear resistance. This means they last longer when handling rough or hard materials. They also handle impact well, which is important in crushers where heavy rocks hit the liner surface.
Another big benefit is heat resistance. In hot processes, these liners won’t break down easily. That makes them a better option than regular steel liners or cast iron in many cases.
Alloy steel liners can be shaped to fit almost any part. That makes them useful for custom jobs or high-load areas. In short, they protect machines, last longer, and help cut down on repair costs.
Step-by-Step Manufacturing Process of Alloy Steel Liners
At Huasuma, our Manufacturing Process ensures precision and quality in every product. From raw material selection to final testing, we utilize advanced technologies and strict quality controls. This ensures our engine parts meet global standards and exceed customer expectations.

1. Raw Material Selection
Raw material is classified based on its chemical composition and stored in individual bins, raw material is transferred from the bins to the furnace manually.
Induction furnaces are used to melt the metal, once the required temperature is obtained a chill sample is prepared and the chemical analysis is checked on a spectrometer.
The main base is alloy steel, but other metals are added to make it stronger.
One popular choice is high-manganese steel. It becomes tougher when exposed to repeated impact. That makes it ideal for crushers. Cr-Mo alloy steel is another option. It offers both strength and heat resistance, which is useful in grinding mills.
For high-wear conditions, some liners include cast iron or high chrome white iron. These materials resist surface damage but may not handle impact as well.
Each alloy has its role. Manganese steel is used where impact is high. Cr-Mo steel works well in places that deal with both heat and wear. White iron gives strong surface protection but is more brittle.
To control the liner’s hardness and toughness, the chemical mix is tested carefully. Small amounts of carbon, chromium, molybdenum, and nickel are adjusted. Even a small shift in one element can affect how the liner performs.
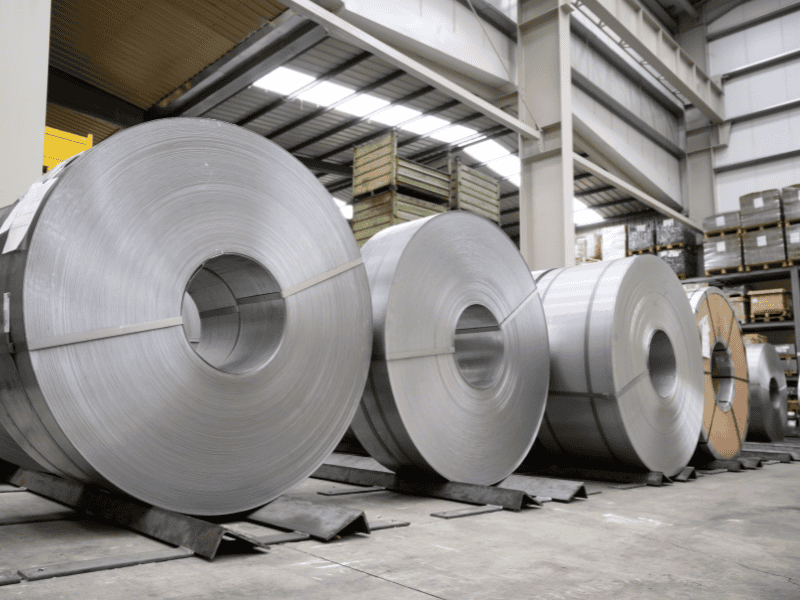
2. Mold Design & Simulation
After picking the right materials, the next step is to design the mold. This mold gives shape to the final liner.
Most manufacturers use CAD software to create the mold design. CAD lets engineers adjust every detail before anything is made. It ensures the liner will match the machine exactly.
To avoid casting problems, a casting simulation is also run. This digital test shows how the metal will flow and cool inside the mold. It helps spot issues like air pockets, weak spots, or cracks before real casting starts.
With the help of simulation, the team can fix problems early. This saves time and improves the final product’s quality.
3. Casting Process
Once the mold design is ready, it’s time to cast the liner. This step turns raw metal into a solid part.
There are a few common casting methods for alloy steel liners. The first is sand casting, where molten metal is poured into a sand mold. It’s widely used for large or heavy parts.
Another method is lost foam casting. This uses foam models that melt away when the hot metal is poured. It helps create more complex shapes with better surface detail.
Centrifugal casting is also used, especially for thick-walled, tubular liners. In this method, the mold spins quickly while the metal is poured. This makes the metal spread evenly and form a strong, dense part.
Each method requires careful mold preparation. The inside of the mold must be clean and shaped well. Temperature control is also key. If the metal is too hot or too cold, the casting may crack or shrink unevenly.
The goal is to get a clean, strong liner with no defects. Choosing the right casting method helps match the shape, size, and strength needed for the job.
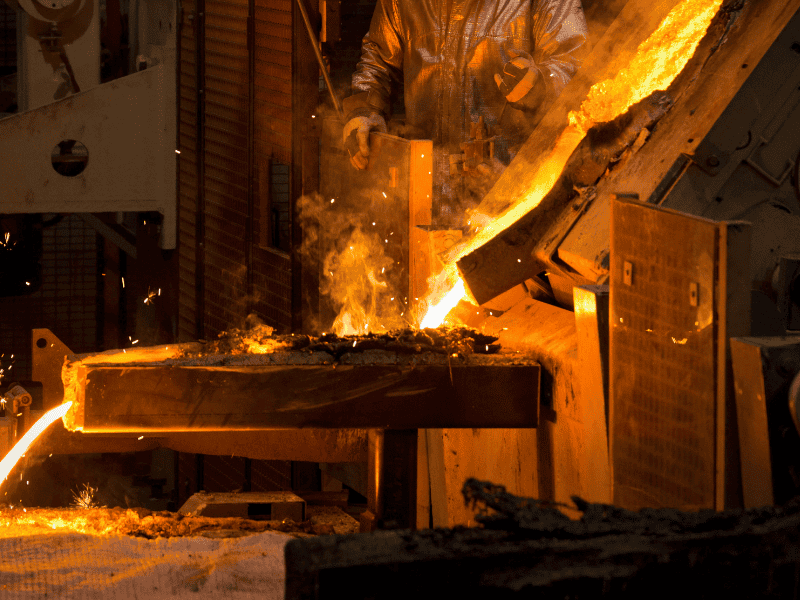
4. Heat Treatment
After casting, the liner must be heat treated to reach the right hardness and strength. This step is key for durability.
The two main heat treatment steps are hardening and tempering. First, the liner is heated to a high temperature and then cooled quickly. This makes the surface harder and more wear resistant.
Next comes tempering. The part is reheated to a lower temperature and then cooled again. This reduces brittleness and adds toughness. The final goal is to reach a hardness level of HRC 50 to 65.
Proper heat treatment helps the liner resist impact and wear. It also improves shape stability under high stress. If skipped or done poorly, the liner may crack or wear out early.
Many manufacturers use controlled ovens or induction systems to manage this step. Temperature and time must be exact. Even small changes can affect the liner’s performance.
5. Machining & Surface Finishing
Once the liner is heat treated, the surface must be finished to meet exact shape and size. This ensures a perfect fit.
CNC machines are used to cut and shape the liner with high accuracy. They help keep the surface flat and smooth. Areas like bolt holes, mating surfaces, and edges must meet tight tolerances to avoid leaks or vibration.
For large liners, Blanchard grinders or surface grinders are used. These tools remove extra material and flatten the surface evenly. The grinding step is key when liners must match with other parts.
Some liners are also polished or shot blasted to clean the surface. Shot blasting removes rough edges and improves bonding if coatings will be applied.
This final step is not just about looks. Smooth and flat liners fit better, last longer, and work more safely under heavy loads.
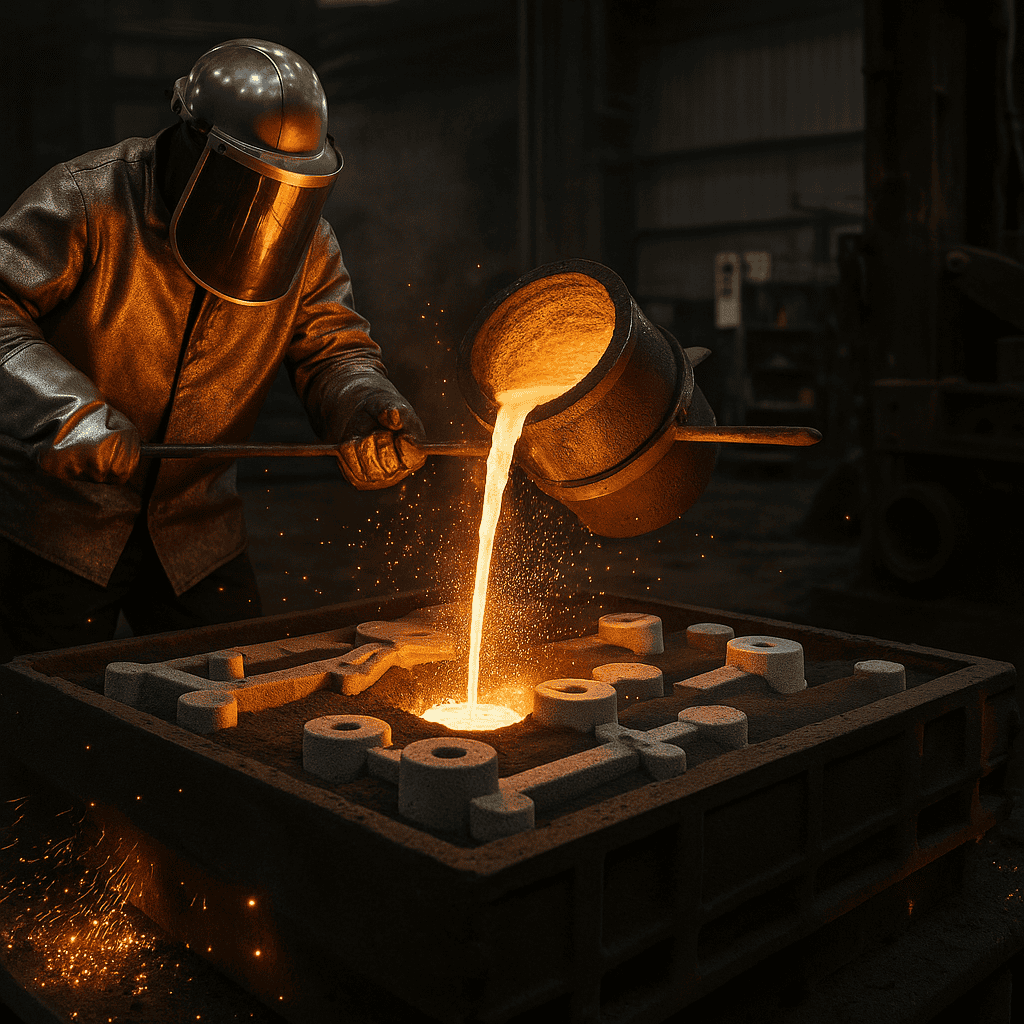
6. Inspection & Quality Control
The first check is for cracks or hidden flaws. Ultrasonic testing (UT) is often used for this. It sends sound waves into the liner and shows if there are air pockets or weak spots. Magnetic particle testing (MT) is also common. It helps find tiny cracks on the surface.
In final inspection stage we maintain & checked all parameter as per standard drawing. We have Digital micrometers, Digital vernier , Boregauge, Roundnesstester & pneumatic Plug gauge, pneumatic ring gauge which fullfill the final inspection criteria.
Key Technologies That Improve Wear Resistance
Wear resistance is a critical property of materials that determines their ability to withstand friction, erosion, and other forms of degradation. Strong liners last longer, work better, and save money.
Microstructure Control
The way a liner cools affects its internal grain structure. A tight, even structure helps reduce cracks and surface wear. Controlling the cooling rate during casting improves strength and keeps the liner stable under stress.
Balanced Alloying Elements
Adding the right amount of chromium, molybdenum, or nickel boosts hardness and impact strength. But too much of any element can weaken the liner. That’s why each batch is tested to keep the mix balanced.
Use of Ceramic Materials
The choice of material plays a significant role in determining wear resistance. Materials with high hardness, such as ceramics and hard metals, tend to exhibit excellent wear resistance. Alloying elements can also be added to enhance wear resistance. These are useful in parts that see constant abrasion, like mill liners and chutes.
Ceramic-Rubber Liners
This design combines ceramic blocks and rubber backing. The ceramic takes the wear, and the rubber absorbs shock. These liners are common in high-wear zones with impact and sliding contact.
Advanced Wear Products and Coatings
Some manufacturers use custom coatings or surface treatments to improve liner life. These include heat-treated surfaces or hard overlays made to resist deep scratches and gouges.
Design Considerations for Wear Resistance
Design considerations play a crucial role in ensuring wear resistance. Some key factors to consider include:
- Component geometry: optimizing the design to minimize stress concentrations and wear.
- Surface finish: ensuring a smooth surface finish to reduce friction and wear.
- Lubrication: ensuring adequate lubrication to reduce friction and wear.
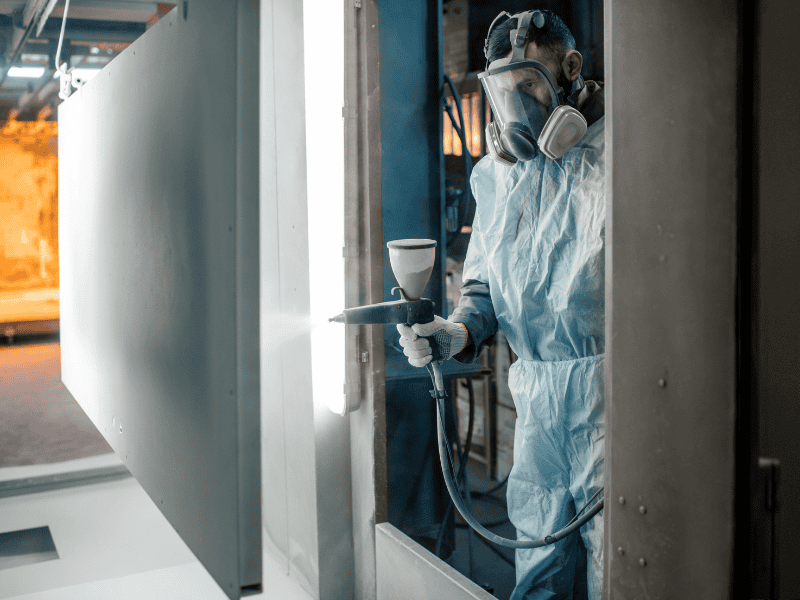
Production Process Comparison: Alloy Steel vs Manganese Steel Liners
Alloy steel and manganese steel are both used to make liners. But they work best in different jobs. Here’s how they compare:
Category | Alloy Steel Liners | Manganese Steel Liners |
Casting Method | Sand, lost foam, centrifugal | Mostly sand casting |
Heat Treatment | Hardening and tempering for control | Natural aging or basic heat treatment |
Best Use | High wear and medium to high impact | High impact with less surface abrasion |
Lifespan | Longer, due to strong wear resistance | Medium, wears faster in abrasive conditions |
Strength | Good mix of hardness and toughness | Tough, work-hardens under impact |
Surface Finish | More options for precision and smooth surfaces | Often rougher, may need post-processing |
When to Choose Alloy Steel Liners
Use alloy steel liners when you need strong wear resistance and better control over size and shape. These liners handle tough loads and abrasive materials well.
When to Choose Manganese Steel Liners
Pick manganese steel liners for jobs with heavy impact but less abrasion. They get tougher over time but may wear down faster on rough surfaces.
Fit for SAG and Autogenous Mills
SAG mill liners and autogenous mills often use a mix. Some parts may use alloy steel for longer life, while others use manganese steel for impact toughness.
Our Manufacturing Capabilities & Quality Assurance
Huasuma produces alloy steel liners that meet high standards from start to finish. Our team handles every step in-house to ensure quality and fast delivery.
Casting Capacity
We can cast liners ranging from 100 kg to 5000 kg per piece. This makes us flexible for both small and heavy-duty parts. Whether you need one liner or a full set, we can meet the demand.
In-House Processes
All key steps — including heat treatment, CNC machining, and final inspections — are done in our facility. This means we control every stage of production. It also helps reduce lead times and avoid delays.
OEM and Custom Production
We support both OEM equipment and custom jobs. You can send us your CAD drawings, and we’ll make liners that match your exact size and specs. Need a liner designed from scratch? Our engineers can help with that, too.
Quality Checks
Each liner goes through strict testing before shipping. This includes ultrasonic testing, dimensional checks, and traceability reports. We follow international standards and provide all the documents you need for quality assurance.
Export-Ready Packaging
Our liners are packed for global shipping. We use secure crates, clear labeling, and add all export documents. That includes material reports, inspection records, and shipping files.
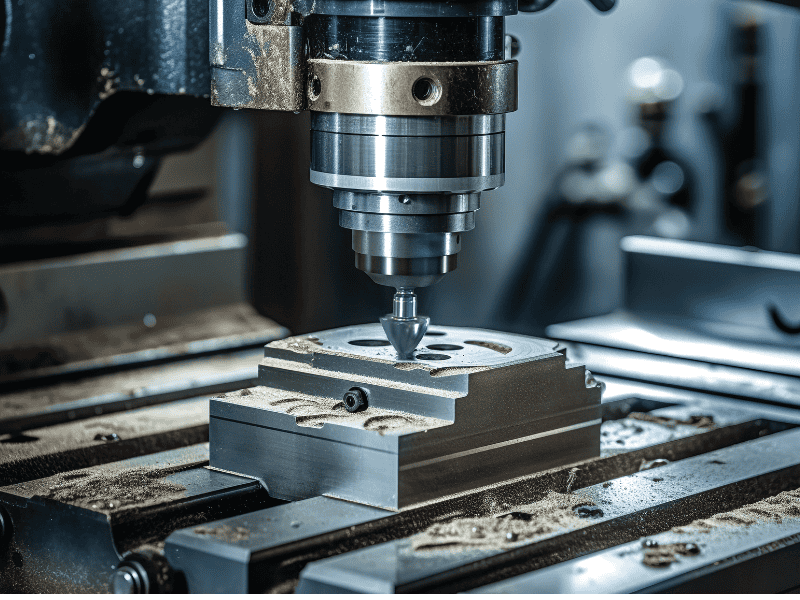
FAQs: Alloy Steel Liner Manufacturing
What’s the typical production lead time?
Most orders take 3 to 6 weeks, depending on the size and quantity. Custom parts or complex liners may take longer. We’ll give you an exact timeline once we receive your drawing and specs.
Do you offer custom alloy compositions?
Yes. We can adjust the metal mix based on your needs. If you require extra toughness, higher heat resistance, or lower weight, our team can recommend a custom alloy that fits your job.
What inspection reports do you provide?
Each liner comes with full documentation. That includes ultrasonic test results, chemical analysis, hardness levels, and dimensional checks. We also include traceability records for every part.
Do your liners meet ASTM or equivalent standards?
Yes. Our liners can meet ASTM A532, ASTM A128, or other global standards. Just tell us your required spec, and we’ll match it.
Can you produce parts for OEM equipment?
Absolutely. We manufacture liners for many OEM machines. Just send your part number or CAD file, and we’ll take care of the rest.
Request a Quote or Sample Today
Need high-performance liners for your mill or crusher? We’re ready to help.
You can send us your drawing, choose from our existing specs, or ask for a custom design. We support fast prototyping, small batch runs, and bulk orders.
Want to test before committing? Ask for a free sample. We’ll help you check fit, finish, and performance.
Our Customer Partner team will guide you from start to delivery. If you have questions about alloy types, standards, or lead times, just let us know.
✔ Get a Free Sample
✔ Submit Your Drawing for Quotation
✔ Talk to Our Technical Team