When industries need a material that’s strong, light, affordable, and resistant to corrosion, aluminum often comes out on top. Its lightweight nature, combined with impressive strength, corrosion resistance, and affordability, makes it a go to material across countless industries. From aerospace and automotive to consumer electronics and industrial equipment, aluminum alloys form the backbone of millions of products worldwide.
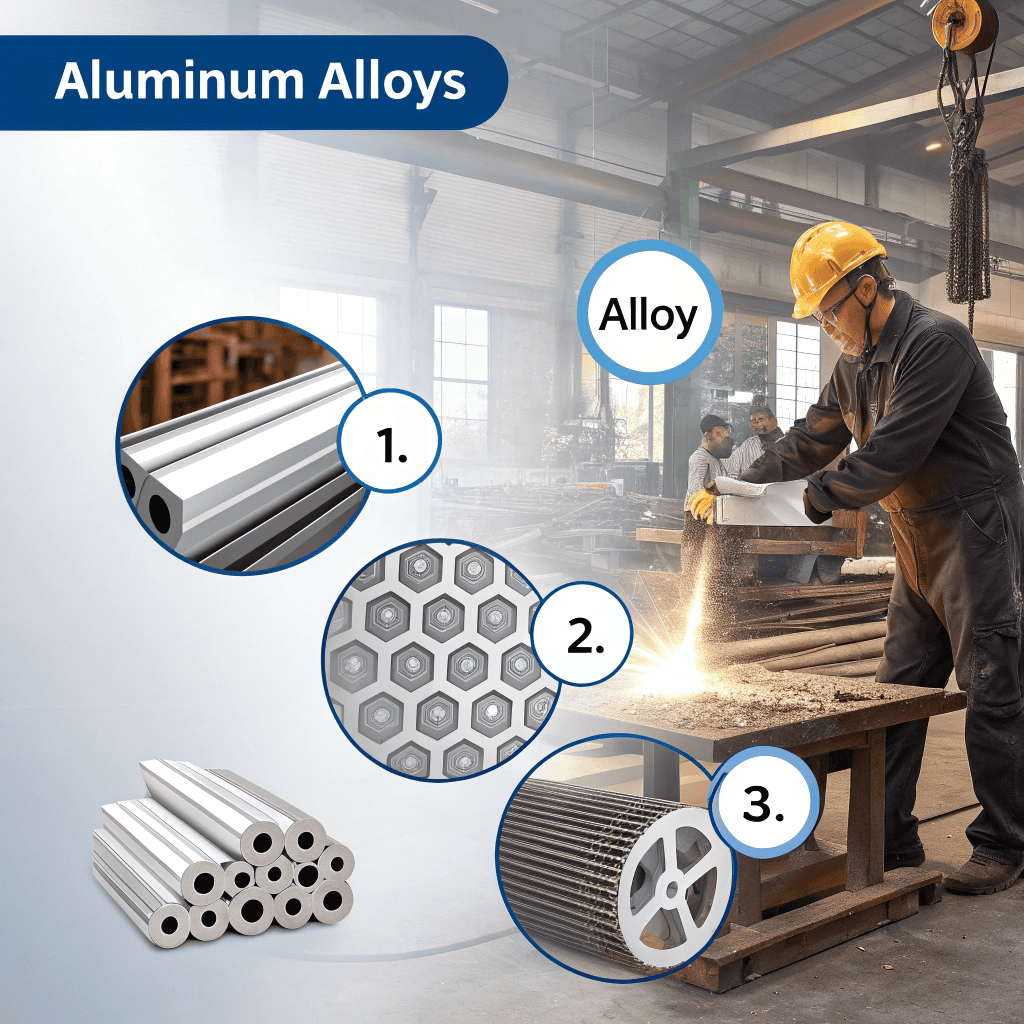
But not all aluminum is created equal. Matching the right aluminum alloy to your project helps you get the perfect balance of strength, weight, and corrosion resistance. Understanding the difference between aluminum and its alloys, and comparing their distinct mechanical properties, corrosion resistance, formability, and cost can mean the difference between a successful product and an underperforming one.
Here I will explore the major types of aluminum alloys, learn the properties of the most common grades, such as Aluminum 6061 vs. Aluminum 7075. And also explain how emerging needs like lightweighting and the use of manganese in alloys are influencing modern design decisions.
What is the Difference Between Alloy and Aluminum?
To understand and compare aluminum and aluminum alloys, it is very important to first differentiate between pure aluminum and the various alloys made from it.
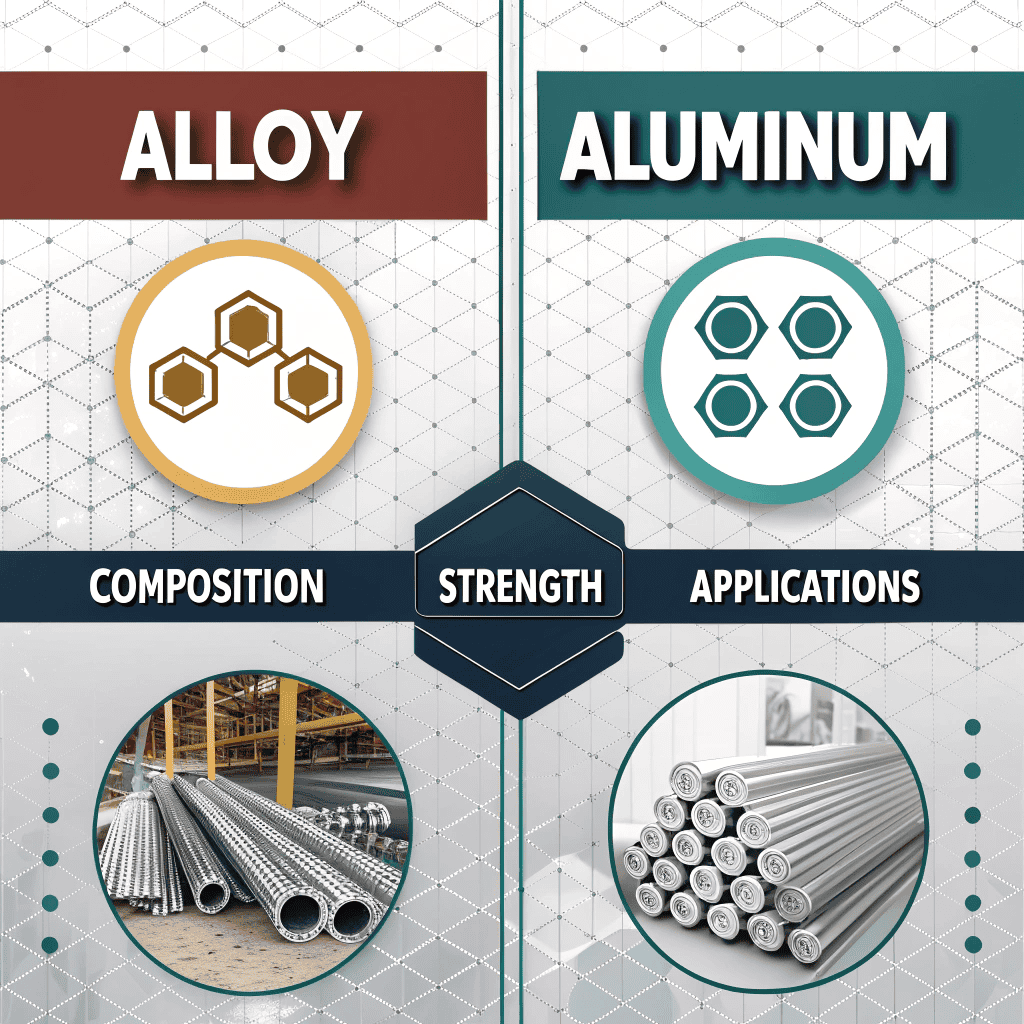
Pure Aluminum: Characteristics and Limitations
Aluminum, in its pure form, is a naturally occurring metallic element known for its remarkable lightweight, malleability, corrosion resistance, and thermal conductivity. Pure aluminum typically contains 99% or more aluminum and is soft and ductile. This makes it easy to work with and shape, but it also limits its application in high stress environments or high load bearing applications.
While pure aluminum is used in some applications, its inherent softness means it is less durable and structurally weak compared to aluminum alloys. This is why, in most industries, pure aluminum is alloyed with other elements to improve its performance characteristics.
Aluminum Alloys: Strength and Durability
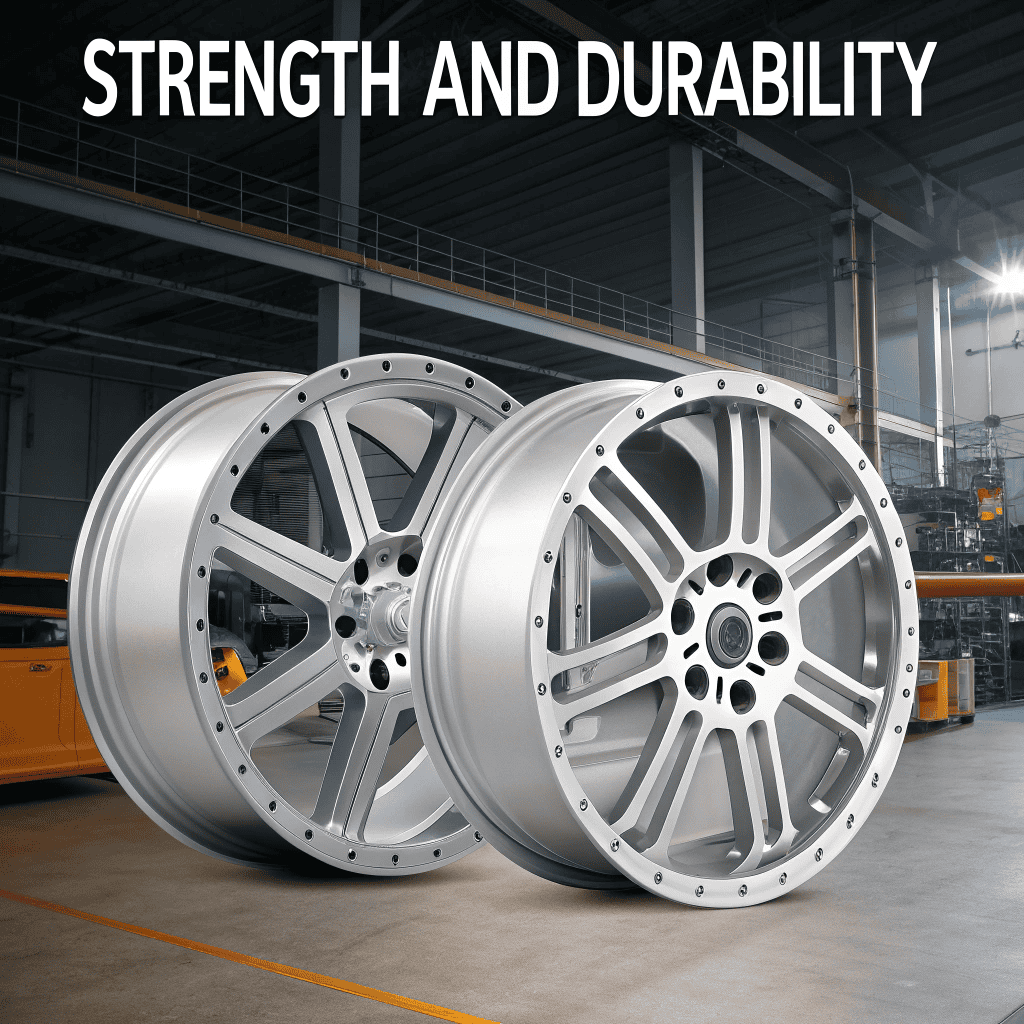
The aluminum alloy we see in everyday products is rarely pure, it is usually combined with other metals like copper, magnesium, silicon, manganese, or zinc to make it tougher and more versatile.
These additions enhance the mechanical properties, strength, hardness, and resistance to wear and corrosion of the metal.
By modifying the alloying elements, engineers can tailor the aluminum’s properties to suit specific applications. Some alloys may have better corrosion resistance, while others may prioritize strength or lightweighting.
Common aluminum alloy compositions are officially recorded by The Aluminum Association. Other groups, like ASTM International and the Society of Automotive Engineers (especially for aerospace), also set detailed standards for how these alloys should be made.
Aluminum alloys are typically divided into two main categories:
- Wrought Alloys: These alloys are created through processes like rolling, extruding, or forging, and are often used in the production of sheet, plate, bar, and rod materials.
- Casting Alloys: These alloys are poured into molds to create parts, often for applications like automotive engine blocks, aerospace components, and consumer goods.
Common Aluminum Alloys and Their Properties
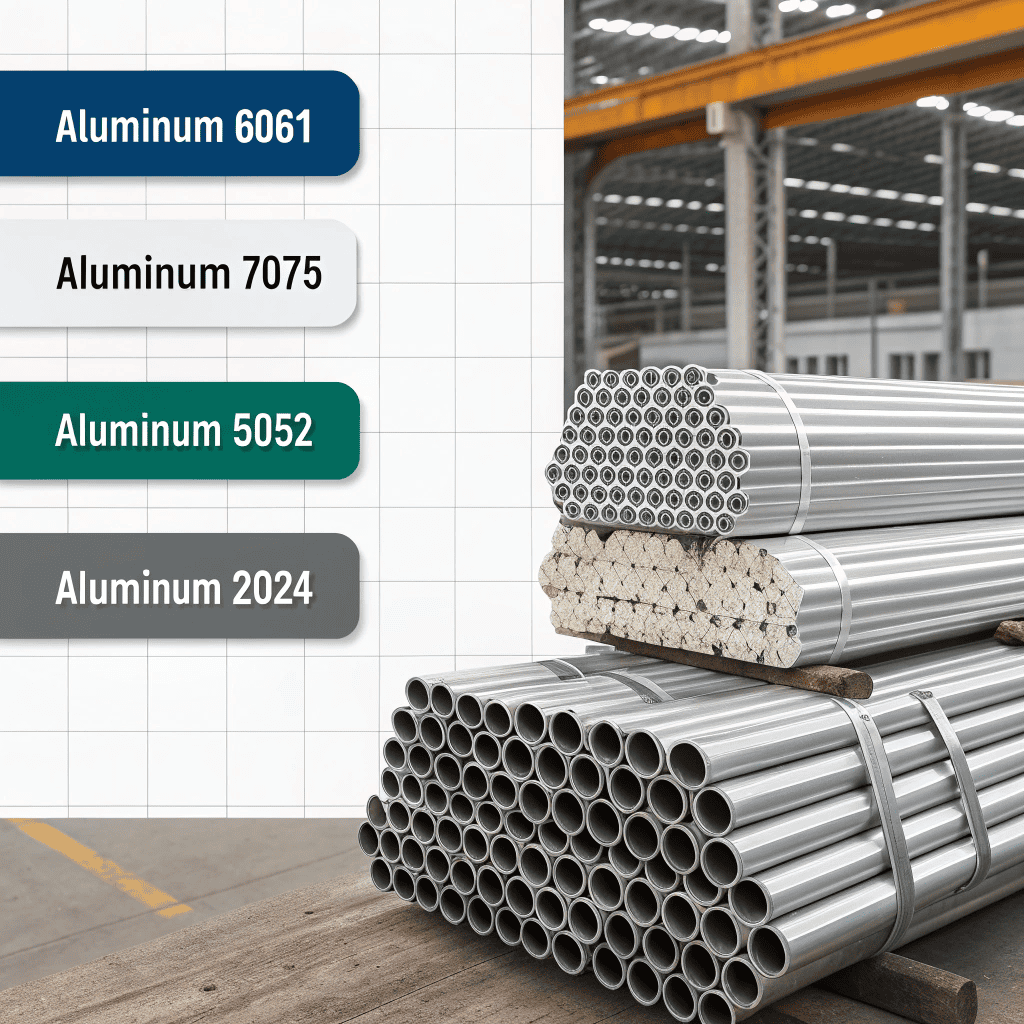
When choosing the right aluminum alloy, the primary factors to consider include strength, corrosion resistance, formability, and cost. Below are some of the most popular and common aluminum alloys and their uses.
Aluminum 6061: The Versatile All Rounder
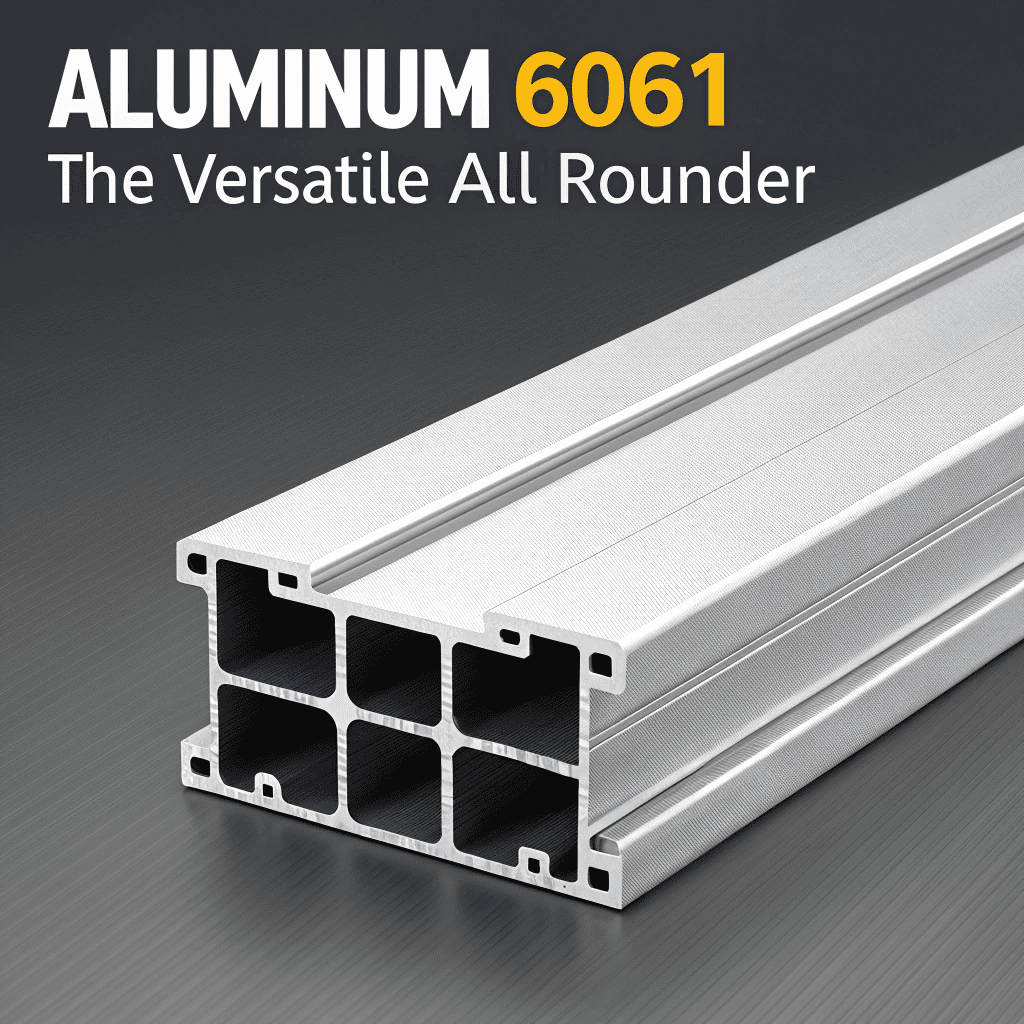
One of the most commonly used aluminum alloys, Aluminum 6061, is known for its excellent balance of strength, corrosion resistance, weldability, and machinability. This alloy is often chosen for applications where good mechanical properties are required, along with ease of fabrication.
Mechanical Properties:
- Tensile Strength: 40 ksi (276 MPa)
- Elongation: 17%
- Hardness: 95 HBW
Applications:
- Automotive parts
- Marine and boat components
- Structural components
- Aerospace applications
- Consumer electronics parts
Advantages:
Aluminum 6061’s weldability and formability make it the alloy of choice for many industries. It is also strong corrosion resistant that allows it to withstand harsh environmental conditions. However, while aluminum 6061 is versatile, it is not the strongest option available, which is why it is not typically used in high performance applications like aerospace or military.
Aluminum 7075: High Strength for Demanding Applications
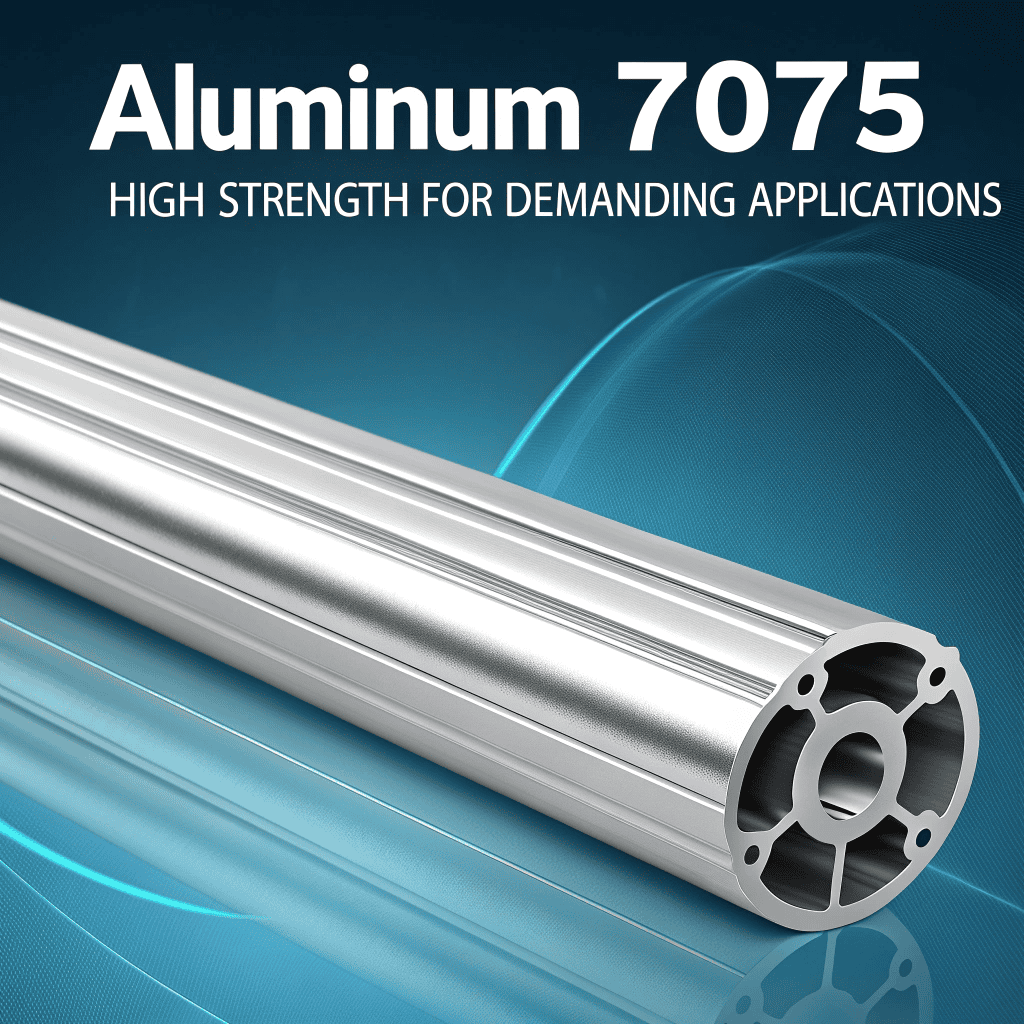
If you need serious strength, Aluminum 7075 is usually the material people trust. This alloy has one of the highest strength to weight ratios among common aluminum alloys and is commonly used in aerospace, military, and performance sporting equipment.
Mechanical Properties:
- Tensile Strength: 83 ksi (572 MPa)
- Elongation: 11%
- Hardness: 85 HBW
Applications:
- Aerospace structures
- Military components
- High performance sporting equipment
- Robotic parts
Advantages:
The biggest advantage of 7075 is that it’s both super strong and lightweight, which is why it is great for handling heavy stress.
However, it has some drawbacks, including poor weldability (due to its susceptibility to stress corrosion cracking) and higher cost compared to alloys like 6061.
Aluminum 5052: Corrosion Resistance for Marine Environments
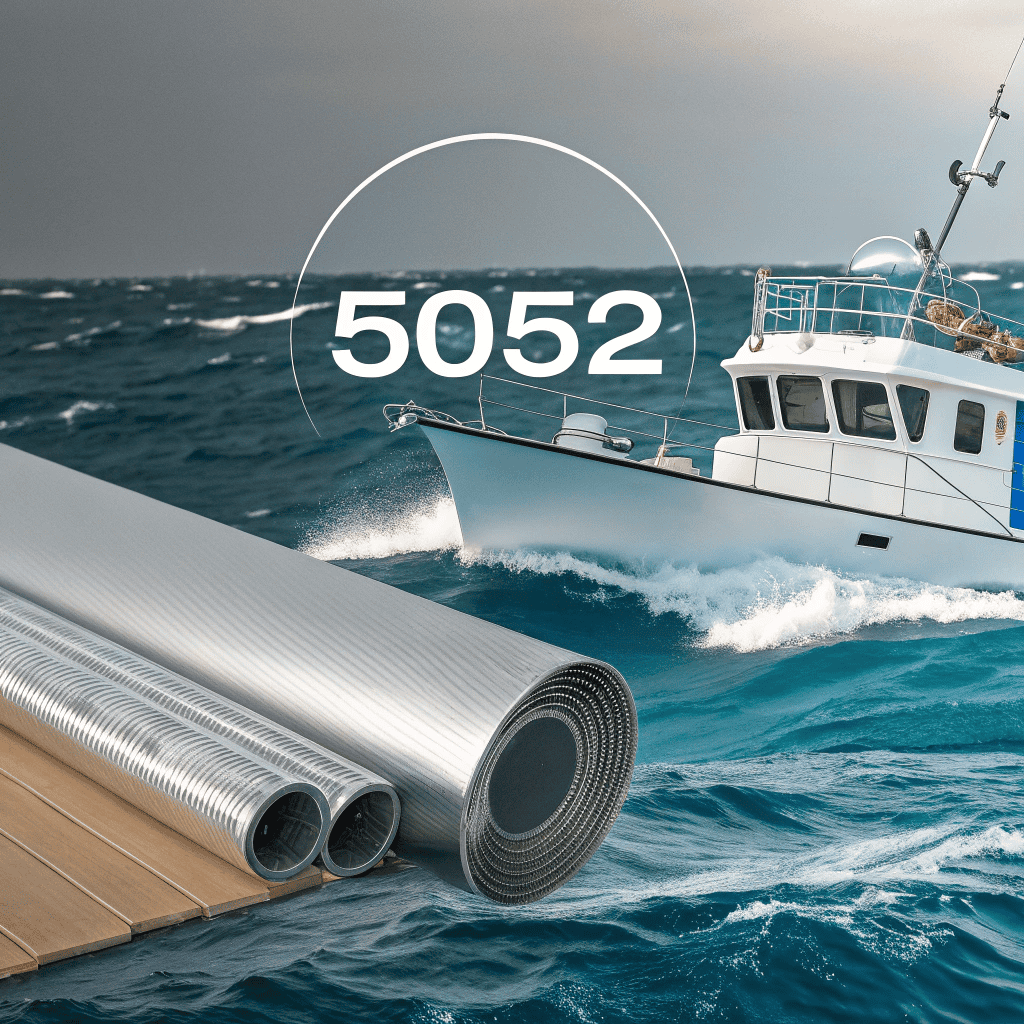
Another commonly used alloy is 5052 aluminum, which is well known for its great corrosion resistance. This makes it a good choice for spare parts that are often exposed to saltwater, chemicals, and tough weather conditions. Although 5052 is not as strong as 6061 or 7075, its ability to resist rust and damage from the environment makes it perfect for marine parts, fuel tanks, and outdoor equipment. It is also easy to shape and weld, which is why it is widely used in many industries.
Mechanical Properties:
- Tensile Strength: 33.34 ksi (228 MPa)
- Elongation: 12%
- Hardness: 60 HBW
Applications:
- Marine and offshore equipment
- Fuel tanks
- Pressure vessels
- Chemical processing equipment
Advantages:
5052 is ideal for use in industries where corrosion is the primary concern. The alloy is also relatively easy to form, which makes it suitable for sheet metal fabrication.
Aluminum 2024: Aerospace and Aircraft Applications
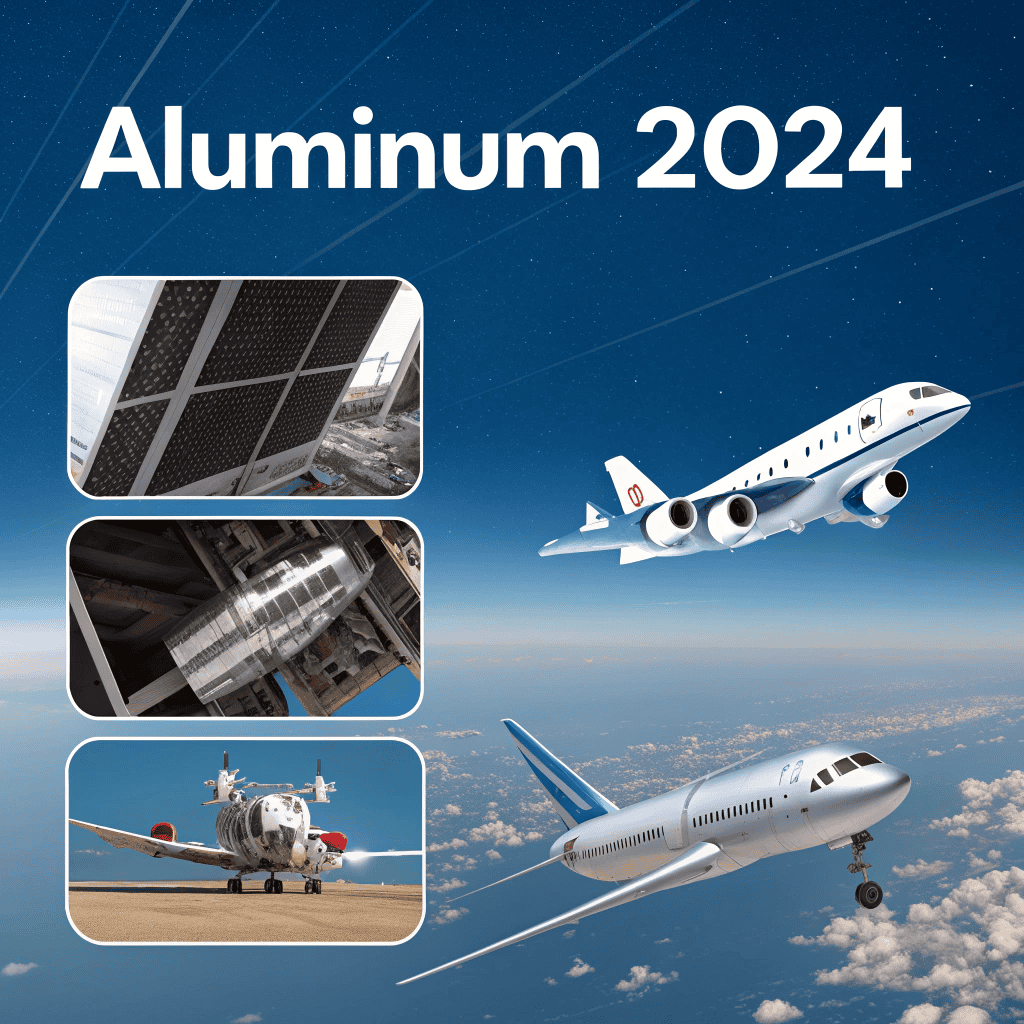
Aluminum 2024 is a high-strength alloy, typically used in aerospace applications that require both strength and lightweight. While it provides excellent fatigue resistance, its corrosion resistance is not as high as other alloys, which limits its use to environments where it is protected by coatings or other corrosion-resistant treatments.
Mechanical Properties:
- Tensile Strength: 68 ksi (469 MPa)
- Elongation: 19%
- Hardness: 120 HRB
Applications:
- Aircraft structures
- Spacecraft components
- Military applications
Advantages:
2024 offers a high strength-to-weight ratio, which makes it a favorite for the aerospace industry. However, its lower corrosion resistance requires careful consideration of the operating environment.
Comparing Aluminum 6061 vs. Aluminum 7075: Which is Right for Your Part?
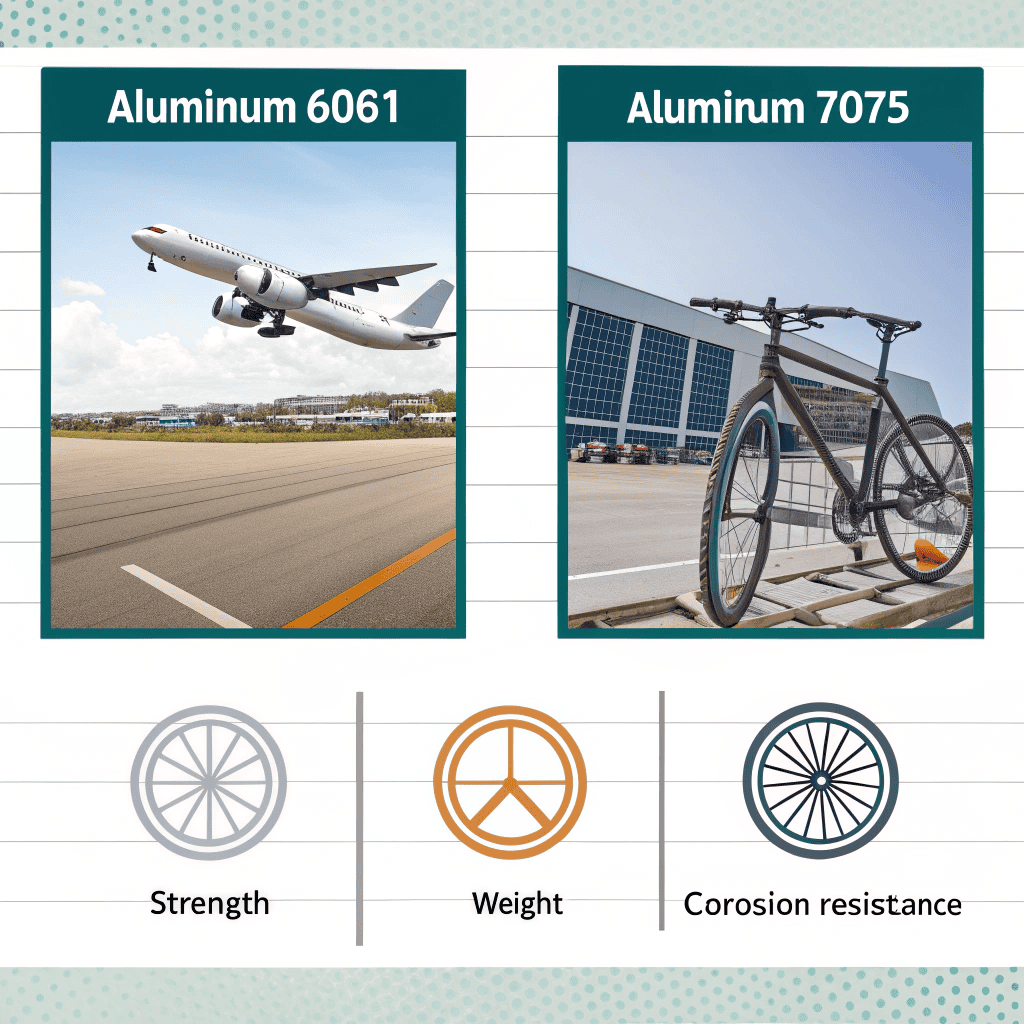
When comparing 6061 and 7075, the key differences lie in strength, weldability, cost, and corrosion resistance.
- Strength: 7075 has significantly higher tensile strength than 6061, making it suitable for high-stress applications.
- Weldability: 6061 is easier to weld, while 7075 can suffer from stress corrosion cracking when welded.
- Cost: The special mix of metals and the extra work required to shape and finish it is what makes 7075 more expensive than 6061.
- Corrosion Resistance: In tough conditions like saltwater or chemical exposure, 6061 holds up better against corrosion than 7075.
Which to Choose?
If you need a part for a high performance application (like aerospace or military), 7075 is the better option due to its strength. However, for general purpose use, especially in environments with exposure to corrosion, 6061 is a more cost effective and versatile choice.
The Role of Manganese in Aluminum Alloys
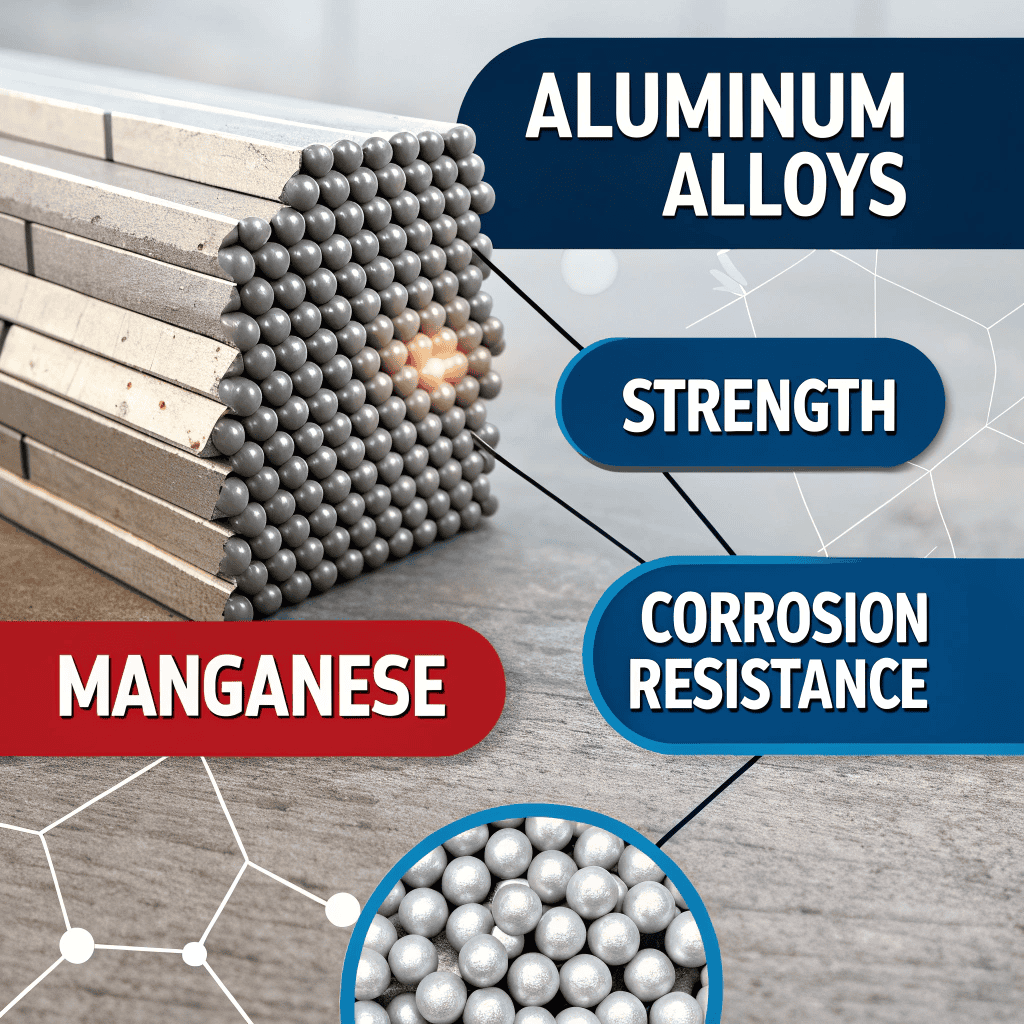
Manganese is a common alloying element in aluminum, used primarily for its ability to improve corrosion resistance, especially in marine environments. It also helps to improve the strength and ductility of the aluminum without significantly affecting its weight.
By adding manganese, engineers can create alloys that balance both strength and durability. Alloys such as 5052 and 5754 contain significant amounts of manganese and are typically used in marine and chemical applications.
Lightweighting in the Automotive and Aerospace Industries
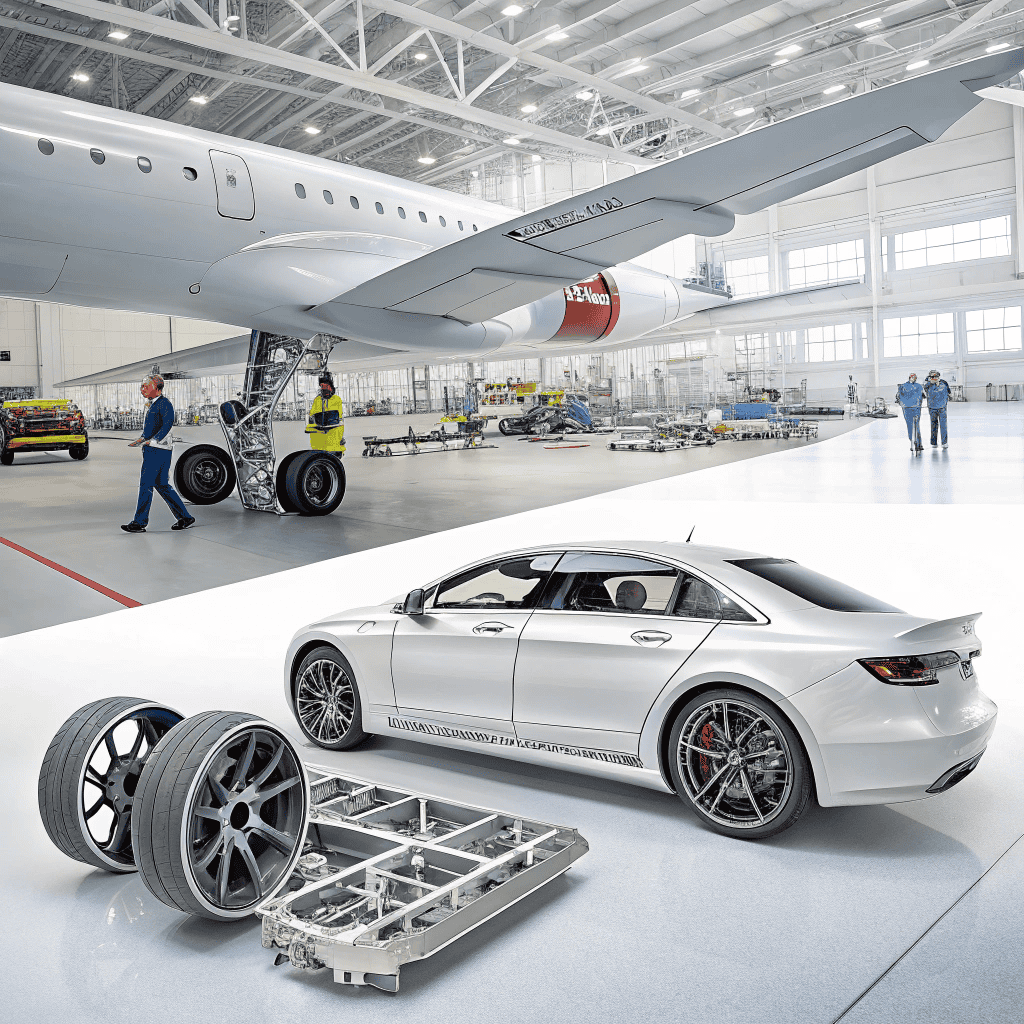
Lightweighting is a crucial trend in industries like automotive and aerospace, as reducing the weight of vehicles and aircraft can directly improve fuel efficiency, reduce emissions, and enhance performance.
Lightweighting is a very old concept. The automotive industry has been using lightweighting to look for ways to reduce weight and costs since the beginning, with aluminum body panels appearing in vehicles as far back as 1909.
In the automotive industry, lightweight aluminum alloys are used to replace steel in car bodies and engine parts, helping manufacturers meet fuel efficiency standards and reduce the environmental impact of vehicles.
In aerospace, the use of aluminum alloys like 7075 and 2024 helps to reduce the weight of aircraft, thereby improving fuel efficiency and allowing planes to carry heavier payloads.
Selecting the Right Aluminum Alloy
Choosing the right aluminum alloy is crucial for ensuring that your product performs as expected and Hanke Construction Machinery Manufacturing Co., Ltd will help you in this. Finding the right alloy is all about balance, means strength, corrosion resistance, formability, weldability, and cost must all work together to meet your part’s needs.
- Aluminum 6061 is a great all-around choice for general-purpose applications where weldability, corrosion resistance, and versatility are important.
- In demanding fields like aerospace and the military, where strength can’t be compromised, Aluminum 7075 is a top pick.
- Aluminum 5052 is the ideal choice for parts exposed to harsh environments, offering excellent corrosion resistance.
By understanding the differences between these alloys, you can make a more informed decision on which material to select based on your product’s needs. Whether you are designing a lightweight automotive part or a high-strength aerospace component, the right aluminum alloy will ensure your part delivers the best possible performance while maintaining cost-efficiency